Es frecuente levantar una soldadura por
errores en el transcurso del trabajo o simplemente por chequear alguna
para verificar el material de aportación, tubo o accesorios. Existe
una técnica para levantar soldaduras que, aplicada, no hay soldadura
que se resista salvo casos muy raros. Esa misma técnica, al contrario
usada, nos servirá para soldar. No son sistemas de feliz idea.
Simplemente aplicar el sentido común.
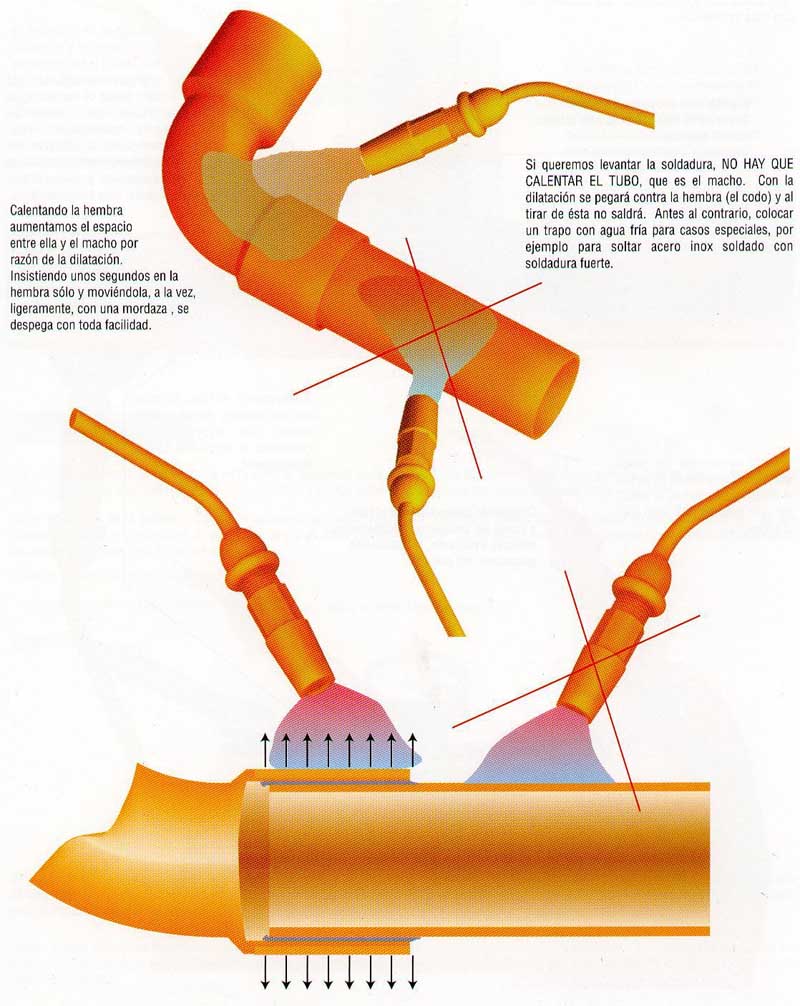
CALENTAR PARA SOLDAR
En página anterior se estudió cómo desoldar un accesorio (codo) de un trozo de tubo. Se verá qué hacer para calentar bien una junta tubo-accesorio, de modo que se suelde adecuadamente.
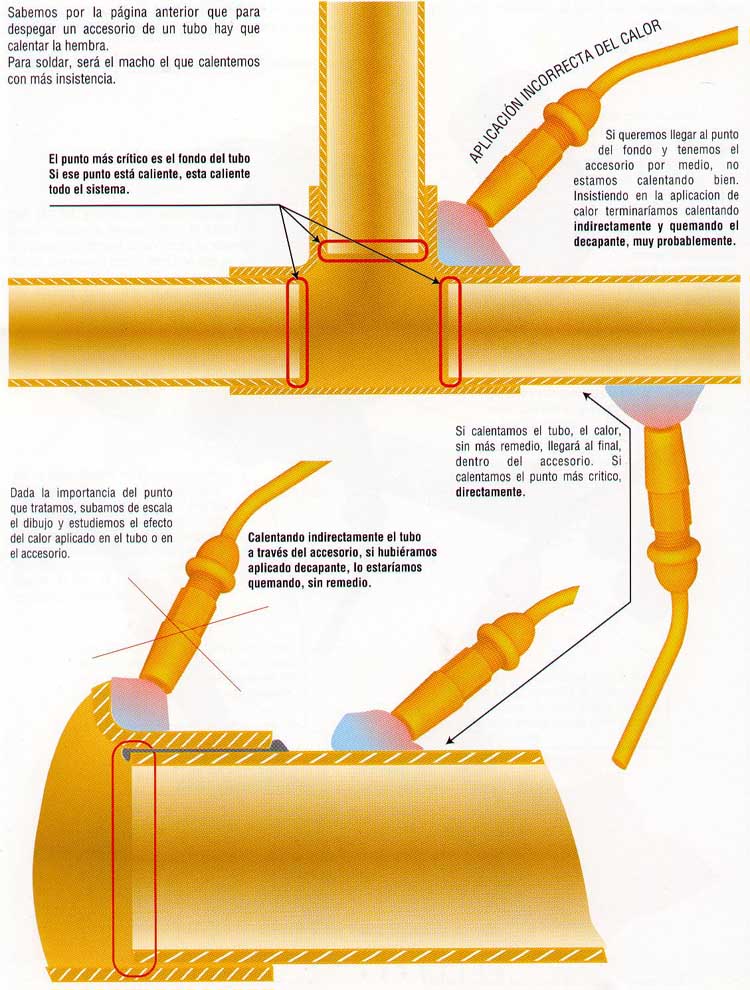
CONCEPTO DE CAPILARIDAD
Para el estudio de la capilaridad en laboratorio se hacen pruebas como la indicada, donde el líquido asciende más en el tubo más fino o entre dos tubos concéntricos. La altura máxima varía con los líquidos pero siempre existe una proporcionalidad inversa: a menor diámetro del tubo más asciende el líquido de prueba. ES UNA PROPIEDAD NATURAL DE LOS CUERPOS EN ESTADO LIQUIDO, ASCENDER POR TUBOS FINOS O ENTRE DOS SUPERFICIES MUY JUNTAS. En soldadura "por capilaridad" se aprovecha dicha propiedad natural.
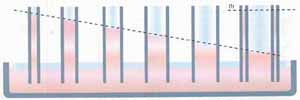
Se gana en capilaridad, a efectos de soldadura del cobre, si sucede: 1 / Distancia mínima entre paredes. El tubo y accesorio deben estar calibrados perfectamente. 2 / Temperatura suficientemente alta y mantenida, para que el material de aportación de la soldadura se mantenga en estado líquido hasta ascender al máximo. 3 / Limpieza química de paredes (decapante) y limpieza mecánica previa, si fuera necesario, para facilitar la ascensión del material de aportación en estado líquido. |
El efecto capilar más expresivo es el
de las plantas. Desde la tierra hacen llegar el agua hasta la hoja más
alta. La ascensión por capilaridad es una PROPIEDAD NATURAL de los
cuerpos en estado LIQUIDO. Si el material es sólido y se llega al punto
de fusión hasta hacerlo líquido, adquiere esta propiedad ascensional.
SE APLICA EN SOLDADURA.
![]() |
![]() |
CORTE DEL TUBO A MEDIDA PARA SOLDAR
El corte del tubo a pesar de los avances
tecnológicos, curiosamente, no está solucionado. Todavía no hay
herramienta mecánica que seccione limpiamente, sin rebabas, a escuadra y
con alto grado de producción. El 95% de los cortes para soldar se dan
en obra, donde no hay facilidades para tener banco, tornillo de
apriete, etc. Además hay que recoger la herramienta cada día por lo que
ésta debe ser mínima y poco voluminosa. Todos los inconvenientes no
son excusa para que el corte sea perfecto de medida, sin comprimir los
labios, sin rebabas y con rapidez, con producción competitiva.
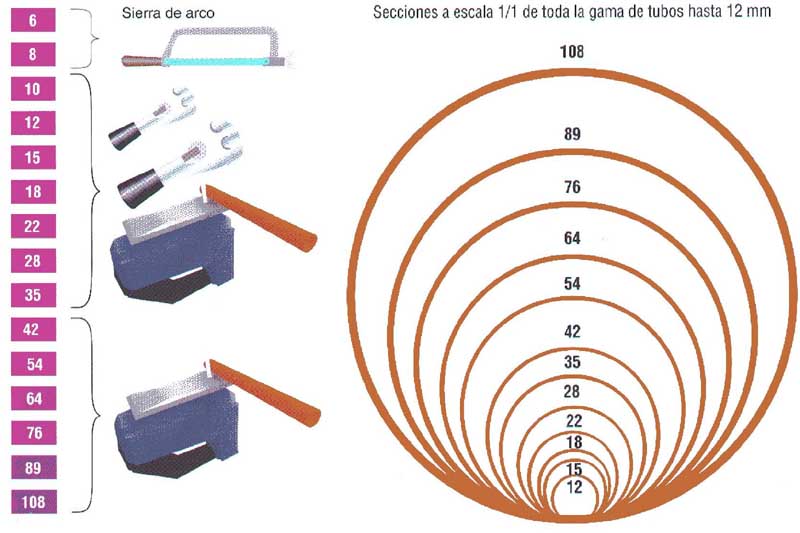
El cortatubo tradicional que llega hasta 22 mm es insustituible para los trabajos de montaje pequeños. Existen varias versiones del cortatubos y todas son útiles y necesarias. El corte con sierra de arco exige la sujeción del tubo, a veces no factible. En la práctica no se usa el arco de sierra: deja rebabas, se tuerce con facilidad, se parte la sierra con la misma facilidad, el cobre se mecaniza muy mal, y frecuentemente embota la sierra. Solamente para tubos capilares de 6 y 8 mm se usará el arco de sierra.
|
![]() |
Solución universal de corte: La sierra de calar.
Existen todo tipo de hojas de sierra que se pueden hacer trabajar a
diversas velocidades manejadas electrónicamente con toda facilidad.
Existen varias longitudes de sierra de corte. El precio de esta
herramienta es muy tolerable. Vale para todos los calibres. Se puede
manejar con una sola mano. Tiene una enorme capacidad de producción,
cincuenta tubos de 15 a 18 mm los corta en tres o cuatro minutos. No
pesa ni abulta mucho. Finalmente puede rebanar dos milímetros a un
tubo, imposible para el cortador estándar.
DECAPANTES
SOLDADURA BLANDA
La función del decapante es
doble: limpieza y ayudar al efecto capilar, "engrasando" las
superficies que han de quedar soldadas. Hasta la llegada de los
decapantes en gel, el bote del ácido parecía destinado a caerse en el
lugar más inoportuno antes que a cumplir su función, por mucho cuidado
que se tuviera. Por lo indicado, es más práctico el decapante en gel.
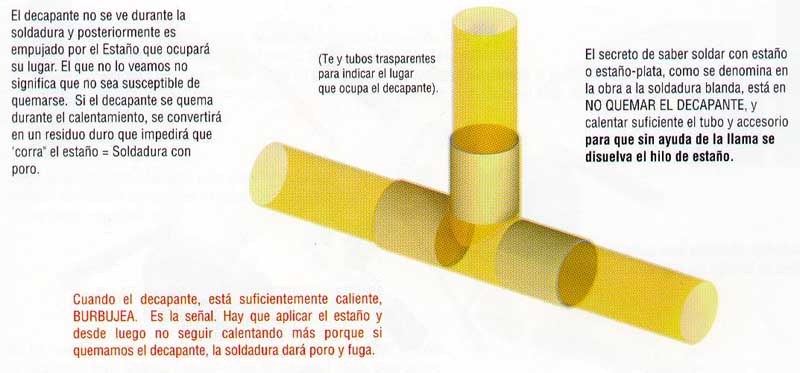
SOLDADURA FUERTE |
Los "polvos de soldar", como se llama
en la obra, al decapante de la soldadura fuerte, parecen todos igual,
pero los buenos son bastante caros y fundamentales para que "corra" la
varilla. Recomendamos probar varias marcas porque hay mucha diferencia
ente unos otros.
Como en el caso de la soldadura blanda, el decapante es fundamental, pero tenemos la ventaja de que se aplica en cada soldadura, no hay que preparar un grupo de juntas antes de soldar, por lo que es difícil quemar una junta. La soldadura fuerte es mas aparatosa por el soplete, el oxígeno, etc, pero más sencilla, más noble que la blanda.
Como en el caso de la soldadura blanda, el decapante es fundamental, pero tenemos la ventaja de que se aplica en cada soldadura, no hay que preparar un grupo de juntas antes de soldar, por lo que es difícil quemar una junta. La soldadura fuerte es mas aparatosa por el soplete, el oxígeno, etc, pero más sencilla, más noble que la blanda.
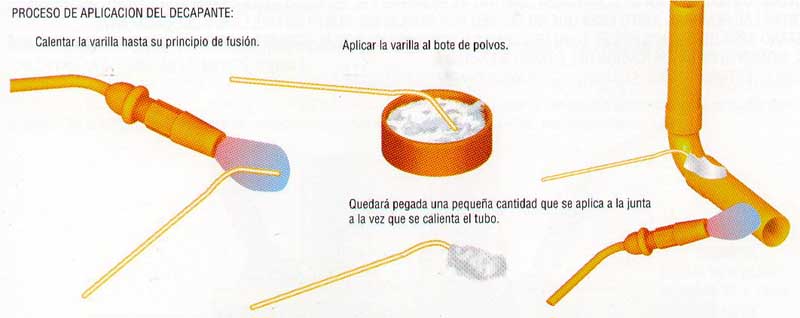
Se puede formar una pasta con polvos y
agua y aplicarla con el dedo o con pincel. No lo recomendamos. El
decapante en polvo se pierde parcialmente si se moja, porque la pasta
obtenida endurece y prácticamente es difícil aprovecharla al 100%. Por
otro lado es bueno ir controlando cada soldadura, tomando del bote
poquito a poquito y aplicando mientras calentamos.
Existen varillas con costra decapante, o sea forradas con los polvos en pasta. Tienen la apariencia de un electrodo. Son un buen sistema, pero hay que tener un enorme cuidado en su manejo y transporte porque al menor golpe la varilla se pela y hay que terminar usando el sistema tópico con las varillas accidentadas.
Existen varillas con costra decapante, o sea forradas con los polvos en pasta. Tienen la apariencia de un electrodo. Son un buen sistema, pero hay que tener un enorme cuidado en su manejo y transporte porque al menor golpe la varilla se pela y hay que terminar usando el sistema tópico con las varillas accidentadas.
DESCINCACIÓN DEL LATÓN, PÉRDIDA DE RESISTENCIA
DESCINCACIÓN del LATÓN, pérdida de resistencia. Estudio de las causas.
El latón se usa en accesorios porque el Zinc le aporta una gran resistencia. Los accesorios que NO han de soldarse es importante que sean de latón y los que han de soldarse, de bronce.
El latón se usa en accesorios porque el Zinc le aporta una gran resistencia. Los accesorios que NO han de soldarse es importante que sean de latón y los que han de soldarse, de bronce.
![]() |
Puede llegar a suceder que la pieza llegue a perder por evaporación el 40% de Zinc que se le aplicó al fabricarla. En el caso del bronce la descincación es muy leve: máximo un 5%, por lo que la pieza mantiene a efectos prácticos su resistencia casi íntegra. |
El Zinc del latón es muy fácil de evaporarse con la temperatura de
soldado. Veanse los datos físicos de los elementos Zn, Cu, Pb y Sn
participantes, en el Latón y/o Bronce. La debilidad del Zinc está en su
punto de evaporación, muy bajo, parecido al de fusión del Cobre, por lo
que, si no se tiene cuidado, en cuando llega la temperatura a 907 ºC
el Zinc comienza evaporarse en forma de humo naranja.
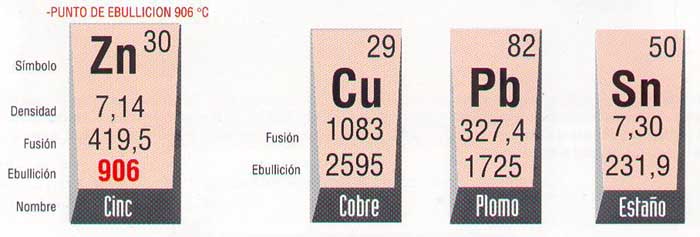
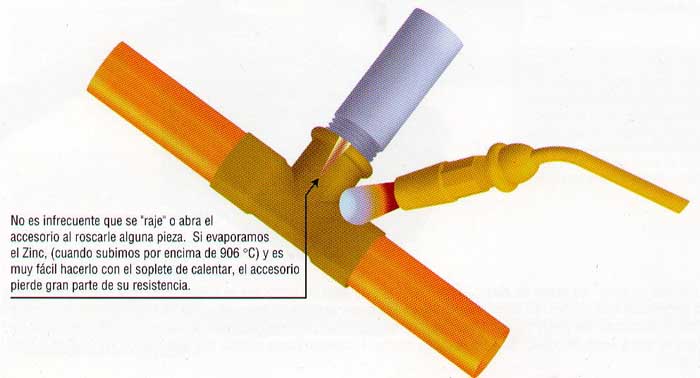
ENFRIAMIENTO DE LA SOLDADURA
El enfriamiento es bien distinto según sea la soldadura, blanda o fuerte.
SOLDADURA BLANDA |
El estaño es un metal blanco argentino, más blando que el cinc, pero más duro que el plomo. A 100ºC es muy dúctil y maleable y puede ser batido en hojas delgadas (papel de estaño). A 200ºC se vuelve muy quebradizo y puede pulverizarse. Funde a 231,8ºC, y hierve a 2270 ºC. El estaño existe en tres modificaciones alotrópicas: formas rómbicas, tetragonal cristalina, y estaño gris, polvo deleznable. Las temperaturas de transición son las siguientes: ![]() |
|
![]() |
El estaño cristalino pasa a gris a temperaturas bajas, inferiores a
18ºC, con tanta más rapidez cuanto menor es la temperatura, alcanzando
un máximo a -50ºC. Se han dado casos de convertirse el estaño en polvo
gris al bajar drásticamente la temperatura.
Podemos observar que el estaño es altamente inestable, por lo que recomendamos no alterar bruscamente. NO ENFRIAR, después de soldar. Sabemos que a veces es imprescidible enfriar, pero que sea el menor número posible y apuntar dichas soldaduras para chequearlas en profundidad durante las pruebas de presión.
Podemos observar que el estaño es altamente inestable, por lo que recomendamos no alterar bruscamente. NO ENFRIAR, después de soldar. Sabemos que a veces es imprescidible enfriar, pero que sea el menor número posible y apuntar dichas soldaduras para chequearlas en profundidad durante las pruebas de presión.
SOLDADURA FUERTE |
Hemos indicado que la soldadura fuerte era "más noble" que la blanda. Incluso para el enfriado esta soldadura se porta noblemente:
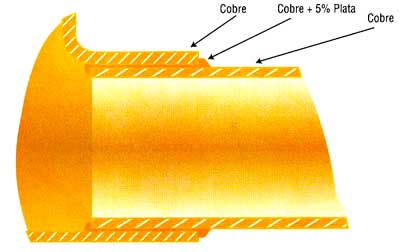
La soldadura fuerte es uniforme, salvo un poco de plata que ayuda a
la capilaridad y no perjudica, porque la plata es de reacciones
parecidas al cobre y el porcentaje es pequeño. Por lo tanto: SE PUEDE
ENFRIAR, SE PUEDE DEJAR DE ENFRIAR Y SE PUEDE ENFRIAR A MEDIAS.
Queremos decir que no importa lo que se pueda hacer: la soldadura, que
es lo que interesa, permanecerá sin alteraciones.
Existe un factor que nadie considera (ningún manual ni cursillo): la seguridad del soldador. Una soldadura recién hecha está a unos 800ºC y no se le nota porque el cobre mantiene su color hasta prácticamente los 1000ºC. Si por descuido o ignorancia se toca la superfície caliente, son 15 días para recuperarse. Una quemadura no es para pedir la baja médica, pero es muy incómoda y resta capacidad. ENFRIAR SIEMPRE QUE SE PUEDA, POR SEGURIDAD. Además craquela y se suelta el decapante, que vitrificó cuando se le subió de temperatura.
Existe un factor que nadie considera (ningún manual ni cursillo): la seguridad del soldador. Una soldadura recién hecha está a unos 800ºC y no se le nota porque el cobre mantiene su color hasta prácticamente los 1000ºC. Si por descuido o ignorancia se toca la superfície caliente, son 15 días para recuperarse. Una quemadura no es para pedir la baja médica, pero es muy incómoda y resta capacidad. ENFRIAR SIEMPRE QUE SE PUEDA, POR SEGURIDAD. Además craquela y se suelta el decapante, que vitrificó cuando se le subió de temperatura.
ESTUDIO DE BOQUILLAS DE SOLDAR Y COMBUSTIBLES
Para que una soldadura sea perfecta, el calentamiento del tubo ha
de hacerse racionalmente. Utilizar una boquilla más adecuada es parte
del proceso de soldadura. El combustible a utilizar es también muy
importante y depende mucho del calibre a soldar.
SOLDADURA BLANDA < 500 ºc (<773 K) |
Para tubo de 12, 15 o 18 mm ha de utilizarse gas butano con cualquier boquilla. ¿Y para un tubo de 54 mm con 2,5 mm de espesor? ¿y para un tubo de 108 mm?. La soldadura "fuerte" destempla el cobre, lo "reduce" y si hay accesorio de latón, este se descinca con facilidad. La soldadura "blanda" bien ejecutada cubre todas las expectativas que la "fuerte" pueda dar.
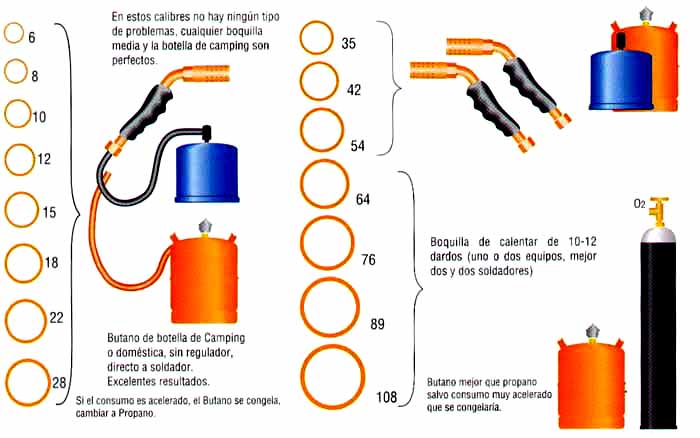
Por razones de seguridad, debe prescindirse del Acetileno en
zonas habitadas. En polígonos industriales o en campo abierto y con
las medidas de seguridad que exige la ley se puede utilizar Acetileno.
La llama reductora y potente de Acetileno es excepcional, pero unas
cinco veces más cara que la de Butano.
SOLDADURA FUERTE 500 ºC ( 773 K) |
La soldadura fuerte necesita calor y solo se puede obtener del Propano-Oxígeno. En caso de no ser importante el factor económico y cumplirse las medidas de seguridad, el Acetileno es ideal. A partir de 54 mm si se quiere rendir habrá que usar dos soldadores y dos equipos.
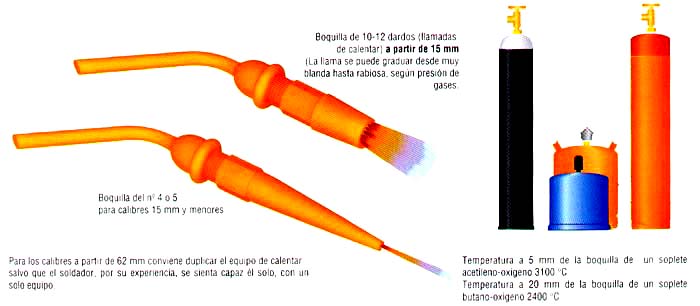
IMPORTANCIA DEL RECALIBRADO DEL TUBO
El corte del tubo recocido conlleva inevitablemente una disminución de diámetro. Si no se aprieta la ruleta, se tarda más y el abollado es menor pero aún así, no resulta tolerable la pérdida de sección. Crea "vicio oculto" en perdida de carga.
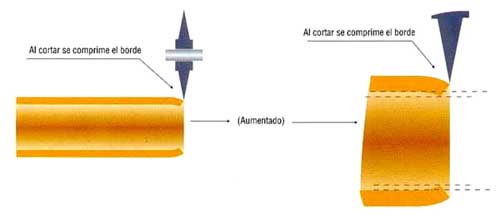
Puede parecer poca cosa, sin importancia,
la abolladura derivada de la presión de la ruleta. Pero si unimos, por
ejemplo, con un manguillo dos tubos se nos presenta una importante
pérdida de carga puntual. Si todas las juntas se han trabajado con el
mismo descuido, ese trabajo u otro habrá salido mal, con Pérdida de
Carga por encima de lo previsto. El dibujo no está exagerado, una rebaba promociona una acumulación de soldadura.
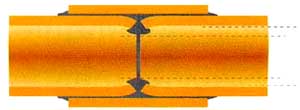
Existen tres métodos para recalibrar: Con calibre a golpeo, con tenaza expandidora y con limatón (lima redonda):
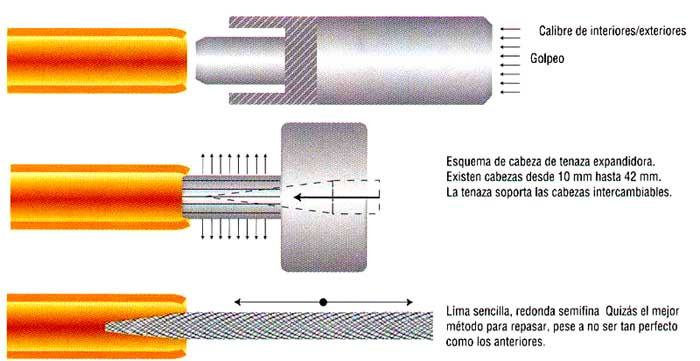
LIMPIEZA DE ZONAS AL SOLDAR
Se puede soldar sin limpiar mecánicamente
el tubo. Con un buen decapante y siguiendo las normas racionales de
soldadura, no hace falta limpiar mecánicamente. Existe implícitamente
en la aplicación del decapante una enérgica limpieza química. Si se
aplica un ácido y luego se le calienta, desde luego la superficie
acidulada queda perfecta de limpieza. Los decapantes: Limpian,
rabiosamente, las zonas a soldar y ayudan a la capilaridad,
desapareciendo del proceso al final. Entonces, ¿Por qué se recomienda
limpiar con lijas, cardas, etc.? Cuestión de "buena vista" del material a
soldar, más que de necesidad. ¿Pero si el tubo está francamente sucio?
¿qué hacemos, cómo limpiamos?. Para el caso de tubo "viejo", o sea,
acumulado en almacén o francamente sucio por causas diversas,
desarrollamos cómo limpiar.
Si el tubo necesita una enérgica limpieza esta no debe perjudicar a la capilaridad:
Si el tubo necesita una enérgica limpieza esta no debe perjudicar a la capilaridad:
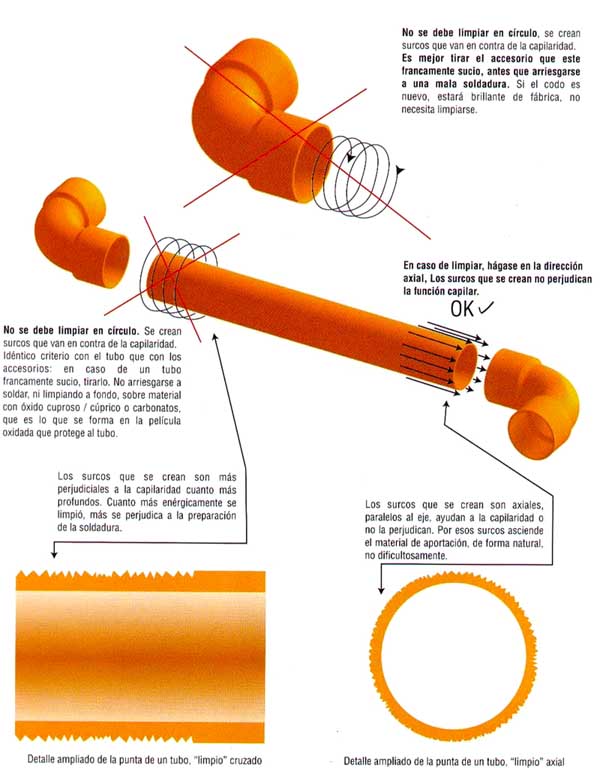
PROCESO DE LA SOLDADURA BLANDA
Se elige el material de aportación, en carrete, con algo de plata, un 4% es suficiente. No se utilizan aleaciones que contengan plomo. La boquilla de soldar es la adecuada, ajustada al diámetro a soldar. Puede ser solo butano o butano y oxígeno, para los diámetros grandes. |
![]() |
Herramienta adecuada para corte de material, también en función del diámetro que se trabaja. | ![]() |
Recalibrar, quitar rebabas y si fuera imprescindible, limpiar mecánicamente el tubo y/o accesorio, sin perjudicar el efecto capilar y aplicar el ácido en gel. | ![]() |
Resumimos:
-CALENTAR LOS MACHOS, ASÍ SE COMPRIMEN CONTRA LAS HEMBRAS Y EL ESPACIO CAPILAR ES MENOR.
-CALENTAR LAS HEMBRAS JUSTO PARA QUE NO QUEDEN POR DEBAJO DEL PUNTO DE EBULLICIÓN DEL DECAPANTE.
-EL ESTAÑO SERÁ DERRETIDO POR EL TUBO DE COBRE CALIENTE, NUNCA POR EL SOPLETE, QUE ESTARÁ LO MAS LEJOS POSIBLE EN EL MOMENTO DE LA APLICACIÓN DEL ESTAÑO A LA JUNTA.
-APLICAR EL ESTAÑO CUANDO EL ÁCIDO (DECAPANTE) COMIENCE A BURBUJEAR.
-CALENTAR LOS MACHOS, ASÍ SE COMPRIMEN CONTRA LAS HEMBRAS Y EL ESPACIO CAPILAR ES MENOR.
-CALENTAR LAS HEMBRAS JUSTO PARA QUE NO QUEDEN POR DEBAJO DEL PUNTO DE EBULLICIÓN DEL DECAPANTE.
-EL ESTAÑO SERÁ DERRETIDO POR EL TUBO DE COBRE CALIENTE, NUNCA POR EL SOPLETE, QUE ESTARÁ LO MAS LEJOS POSIBLE EN EL MOMENTO DE LA APLICACIÓN DEL ESTAÑO A LA JUNTA.
-APLICAR EL ESTAÑO CUANDO EL ÁCIDO (DECAPANTE) COMIENCE A BURBUJEAR.
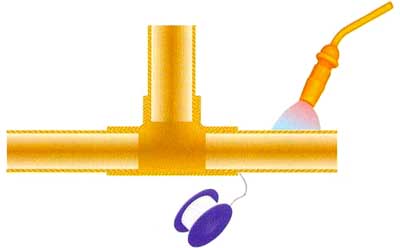
PROCESO DE LA SOLDADURA FUERTE
Aquí se resume cómo ejecutar una soldadura perfecta:
-El material de aportación, en varilla, con 5% de plata es adecuado, salvo casos muy puntuales. Tener siempre reservas, no dejar el pedido hasta la última varilla. El decapante en polvo debe ser cuidadosamente elegido, de la máxima calidad. Es bueno usar del mismo tipo que utilizan los joyeros para los metales preciosos. | ![]() |
-La boquilla debe ser de dardo múltiple, de calentar. Si se da la presión de 0,5 bar al oxígeno y lo máximo que permita el propano o butano, queda una llama adecuada. Repasar el equipo de soldar, de posibles fugas de gas, con agua jabonosa. Esto debe hacerse a diario al menos, si usamos Acetileno. | ![]() |
Elegir la herramienta adecuada para corte de material, también en función del diámetro a seccionar y la obra (nº de piezas repetidas, etc.). | ![]() |
No hay que limpiar mecánicamente, porque al llegar casi a 1000ºC con el decapante, éste, arranca cualquier tipo de suciedad. Sólo para casos excepcionales, limpiar mecánicamente en sentido axial. | ![]() |
Asegurarse en el almacén donde se compra, que los accesorios son de BRONCE. NO deben ser de LATÓN ya que aplicando con la llama más de 906ºC, se evapora el Zinc. | ![]() |
Resumiendo:
-CALENTAR LOS MACHOS, ASÍ SE COMPRIMEN CONTRA LAS HEMBRAS Y EL ESPACIO CAPILAR ES MENOR.
-CALENTAR LAS HEMBRAS LO MENOS POSIBLE.
-LA VARILLA SERÁ DERRETIDA POR EL TUBO DE COBRE O ACCESORIO, NUNCA POR EL SOPLETE. ESTE ESTARÁ LO MAS LEJOS POSIBLE EN EL MOMENTO DE LA APLICACIÓN DE LA VARILLA A LA JUNTA. Evitar el lamentable espectáculo del soldador derritiendo alrededor de la junta la varilla a base de sopletazos, creando soldaduras de buena vista, vacías por dentro.
-CALENTAR LOS MACHOS, ASÍ SE COMPRIMEN CONTRA LAS HEMBRAS Y EL ESPACIO CAPILAR ES MENOR.
-CALENTAR LAS HEMBRAS LO MENOS POSIBLE.
-LA VARILLA SERÁ DERRETIDA POR EL TUBO DE COBRE O ACCESORIO, NUNCA POR EL SOPLETE. ESTE ESTARÁ LO MAS LEJOS POSIBLE EN EL MOMENTO DE LA APLICACIÓN DE LA VARILLA A LA JUNTA. Evitar el lamentable espectáculo del soldador derritiendo alrededor de la junta la varilla a base de sopletazos, creando soldaduras de buena vista, vacías por dentro.

QUE ES LA SOLDADURA BLANDA
Hay dos tipos de materiales de aportación para soldadura: los que se
utilizan en soldadura "blanda" y los usados en la "fuerte". Las
palabras "blanda" y "fuerte" están contempladas en el Reglamento de
Instalaciones de Gas en locales destinados a usos Domésticos Colectivos o
Comerciales (RIGLO):
INSTRUCCIONES TÉCNICAS COMPLEMENTARIAS: Instrucción Técnica Complementaria (I.T.C.) MI-IRG 01. Terminología
01. 42 Soldadura blanda: Es aquella soldadura en la que la temperatura de fusión del metal de aporte es inferior a 500ºC.
01. 43 Soldadura fuerte: Es aquella soldadura en la que la temperatura de fusión del metal de aporte es igual o superior a 500ºC.
Antes de estudiar el tipo de material a utilizar en soldadura blanda, conviene recordar que lo que de ningún modo ha de hacerse es: soldar con barra de Estaño-Plomo. El Reglamento de Instalciones de Gas (RIGLO) lo indica expresamente en la ITC 02.3.2.2. en el último párrafo: "Queda prohibida la soldadura "blanda" con aleación de estaño plomo". La única aleación estándar de Estaño-Plomo existente en el mercado es la barra de soldar para Plomo-Plomo que lleva Estaño en porcentaje entre 15 y 30%.
Datos base del Estaño y de la Plata. Estudio de su uso en soldadura blanda como materiales de aportación en aleación:
INSTRUCCIONES TÉCNICAS COMPLEMENTARIAS: Instrucción Técnica Complementaria (I.T.C.) MI-IRG 01. Terminología
01. 42 Soldadura blanda: Es aquella soldadura en la que la temperatura de fusión del metal de aporte es inferior a 500ºC.
01. 43 Soldadura fuerte: Es aquella soldadura en la que la temperatura de fusión del metal de aporte es igual o superior a 500ºC.
SOLDADURA BLANDA < 500 ºC (<773 k) |
Antes de estudiar el tipo de material a utilizar en soldadura blanda, conviene recordar que lo que de ningún modo ha de hacerse es: soldar con barra de Estaño-Plomo. El Reglamento de Instalciones de Gas (RIGLO) lo indica expresamente en la ITC 02.3.2.2. en el último párrafo: "Queda prohibida la soldadura "blanda" con aleación de estaño plomo". La única aleación estándar de Estaño-Plomo existente en el mercado es la barra de soldar para Plomo-Plomo que lleva Estaño en porcentaje entre 15 y 30%.
Datos base del Estaño y de la Plata. Estudio de su uso en soldadura blanda como materiales de aportación en aleación:
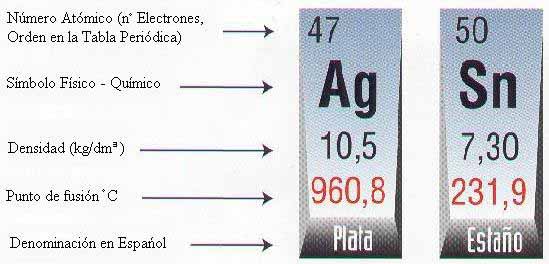
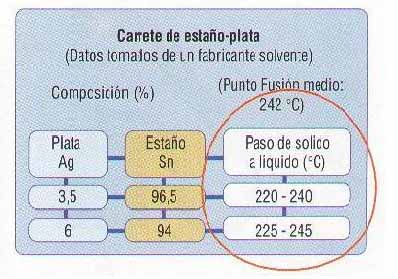
Se observa que el punto de fusión de la aleación es superior al del Estaño solo.
Es por la Plata; significa que a mayores cantidades de Plata mayor
será el punto de fusión. Un punto de fusión alto significa más tiempo
de soldadura, más peligro que quemarse el decapante y los objetos
alrededor de la soldadura. Por lo tanto la Plata ayuda, por su
tendencia natural al efecto capilar, pero no es recomendable mucha en
soldadura blanda, pues lo que se gana en capilaridad se pierde en un
mayor aumento de temperatura. Por las pruebas realizadas se puede
afirmar que no es necesaria Plata soldando Cobre-Cobre si si prepara y
calienta bien el material. Para cobre con accesorio de bronce, es bueno soldar con aleación de un 2 a 5% de Plata.
Para saber, exactamente, qué porcentaje de plata nos venden basta con pesar el carrete y medir su volumen geométricamente. Un litro de Estaño puro debe pesar 7,30 kg exactamente. Un litro de Plata debe pesar 10,5 kg exactamente. Si 1 kg de aleación de Sn-Ag pesa 7,90 kg el exceso de 7,3 a 7,9 es por la Plata. Si se tiene la curiosidad, es fácil calcular los porcentajes exactos de Sn y Ag.
Para saber, exactamente, qué porcentaje de plata nos venden basta con pesar el carrete y medir su volumen geométricamente. Un litro de Estaño puro debe pesar 7,30 kg exactamente. Un litro de Plata debe pesar 10,5 kg exactamente. Si 1 kg de aleación de Sn-Ag pesa 7,90 kg el exceso de 7,3 a 7,9 es por la Plata. Si se tiene la curiosidad, es fácil calcular los porcentajes exactos de Sn y Ag.
QUE ES LA SOLDADURA FUERTE
Hay dos tipos de materiales de aportación para soldadura: los que se
utilizan en soldadura "blanda" y los usados en la "fuerte". Las palabras
"blanda" y "fuerte" están contempladas en el Reglamento de
Instalaciones de Gas en locales destinados a usos Domésticos Colectivos o
Comerciales (RIGLO):
INSTRUCCIONES TÉCNICAS COMPLEMENTARIAS: Instrucción Técnica Complementaria (I.T.C.) MI-IRG 01. Terminología
01. 42 Soldadura blanda: Es aquella soldadura en la que la temperatura de fusión del metal de aporte es inferior a 500ºC.
01. 43 Soldadura fuerte: Es aquella soldadura en la que la temperatura de fusión del metal de aporte es igual o superior a 500ºC.
INSTRUCCIONES TÉCNICAS COMPLEMENTARIAS: Instrucción Técnica Complementaria (I.T.C.) MI-IRG 01. Terminología
01. 42 Soldadura blanda: Es aquella soldadura en la que la temperatura de fusión del metal de aporte es inferior a 500ºC.
01. 43 Soldadura fuerte: Es aquella soldadura en la que la temperatura de fusión del metal de aporte es igual o superior a 500ºC.
SOLDADURA FUERTE 500 ºC ( 773 K) |
Se dan dos casos: Cobre-Cobre, o sea tubo de Cobre con accesorio de cobre, y Cobre-Bronce, (Cobre con piezas soldar/ roscar). La experiencia indica que la soldadura más fuerte, casi autógena, es la que se hace con Bronce Fosforoso (es muy difícil de desmontar). El Bronce Fosforoso es una curiosa mezcla de Cobre y Fósforo blanco. Al aplicar la varilla "se enciende" el Fósforo, como microcerillas, desapareciendo y aumentando la temperatura de la varilla que se disuelve con rapidez por la junta de Cobre-Cobre. El Bronce Fosforoso es el pariente pobre de la soldadura, pero noble, barato y de buen resultado. Se aporta información sobre el Bronce Fosforoso, procedente de una firma de solvencia en aleaciones:
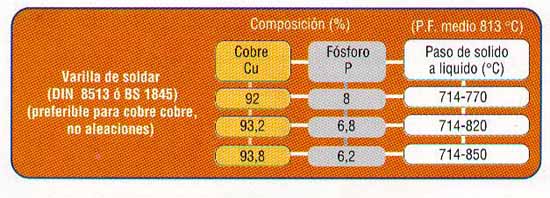
Para los casos en los que se suelda Cobre (el tubo) con Bronce (las
piezas complementarias) es imprescindible una pequeña cantidad de
Plata. Se aconseja el 5%. Observese, además, que en el
catálogo de materiales de una casa solvente en aleaciones el 5%
necesita MENOS temperatura que el 15% de Plata. Se aporta Fósforo
porque ayuda (mucho) en el momento de la fusión de la varilla.
Observese como con tecnología no hace falta tanta Plata. Para piezas de gran masa, en alta presión (300 bar o más), sugerimos hacer pruebas con graduaciones del 30 o 40% en Plata. Estos altos porcentajes de plata aleada en aportación, también se usan para piezas soldadas que hayan de plegarse o mecanizarse pero serían un derroche imperdonable por ejemplo en redes, para presiones de 4 bar o menos. |
![]() |
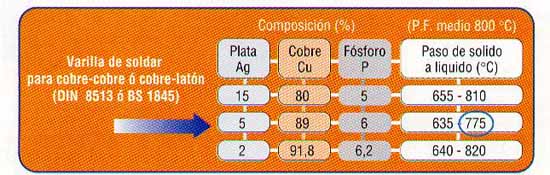
TEMPERATURAS DE FUSIÓN DE ALGUNOS ELEMENTOS DE LA TABLA PERIÓDICA
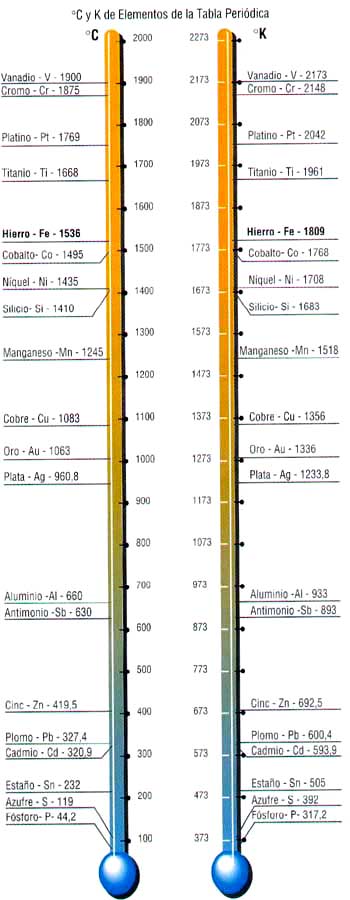
al soldar un tubo de 5/8 a uno de 3/4 sin reduccion o manguito es perjudicial introducir mucha cantidad del tubo de menos diametro
ResponderEliminarpuede producir alguna averia por este motivo en el compresor
ResponderEliminar