AVERÍAS EN CALDERAS DE CHAPA DE ACERO
El mercado de las calderas de acero ha sido creciente durante los últimos años.
Durante este tiempo se han venido produciendo una serie de averías que a priori han provocado en algunos casos la insatisfacción del usuario, así como del instalador.
Las calderas de acero requieren, al igual que otros productos, un mínimo de atenciones, tanto en la fase de montaje como en el periodo de funcionamiento. Como consecuencia de ello, en su momento, publicamos una Monografía específica de calderas de acero, cuyo objetivo era el de dar a conocer todos aquellos requisitos que deben tenerse en cuenta para una correcta instalación.
A pesar de ello, se siguen efectuando instalaciones incorrectas que acortan la vida de estas calderas.
Un porcentaje muy elevado de las averías que se producen en las calderas de acero podían haberse evitado
si se hubiesen seguido las instrucciones mínimas que ofrecemos en nuestras publicaciones. Tratándose de un tema polémico a la hora de hallar la causa
de la avería, hemos creído oportuno exponer aquellas averías mas frecuentes y las causas que las han provocado.
El 95% de las averías no son imputables a defecto del producto. |
- Fugas de agua por la soldadura de los tubos con las placas frontal o posterior.
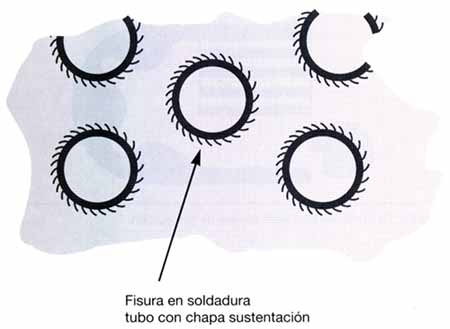
Figura 6.1. Fisuras en tubos.
Causa
- Si la
caldera hace poco tempo que esta en funcionamiento, la avería es debida a
una soldadura mal efectuada con grietas o poros no detectados durante
la prueba hidráulica.Si la caldera lleva mas tiempo en funcionamiento, ver avería - 2.
Avería - 2
- Fisuras o grietas en las placas de sustentación del haz tubular frontal o posterior.
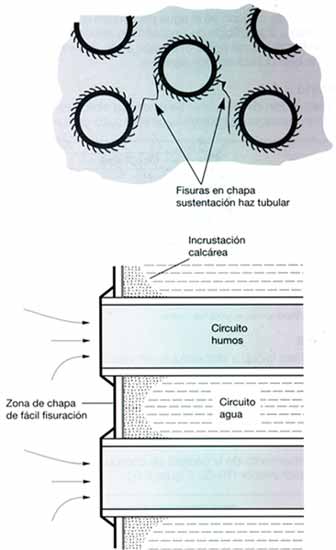
Figure, 6.2. Fisuras en placas sustentación haz tubular.
Causa
- Incrustaciones calcáreas junto a la unión de los tubos y las placas. Cuando esta incrustación tiene un espesor mayor de 3 cm, la chapa no se refrigera y sufre un sobrecalentamiento que produce las fisuras o grietas antes reseñadas.Avería - 3
- Perforación de los tubos. No aparecen síntomas de suciedad en el circuito de humos, lo que podría hacemos pensar en corrosiones por condensaci6n. Extraído el tubo, aparecen cráteres de oxidación en la zona del agua (figura 6.3).
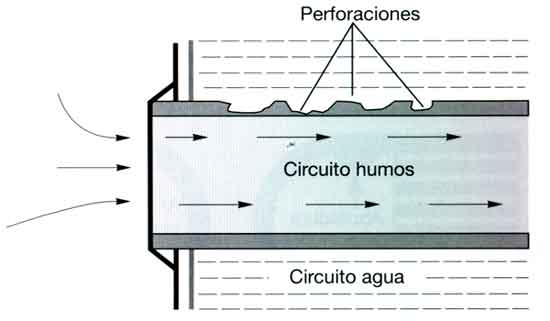
Figura 6.3. Perforaciones en tubos lado agua.
Causa
-
Exceso de oxigeno en el agua del circuito de calefacción debido a la
utilización de deposito expansión abierto jun con la calidad del agua.
Si es algo ácida (pH menor de 7) y de baja dureza es muy agresiva.
Avería - 4
- Perforación de los tubos. Se evidencia síntomas de incrustaciones corrosivas en el circuito de humos.
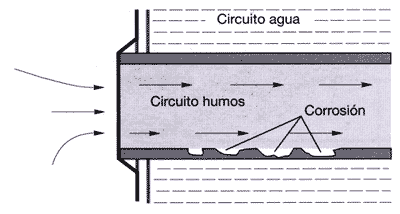
Figura 6.4. Perforaciones en tubos lado humos.
Causa- La caldera trabaja a temperaturas demasiado bajas, provocando condensaciones. El agua producida por las condensaciones se combina con el azufre que contiene el combustible, originando ácido sulfúrico, el cual ataca la chapa.
Se producen unas incrustaciones corrosivas de color amarillo.
Avería - 5
- Abombamiento de la cámara de combustión en su parte posterior inferior (TR-3). (Figura 6.5.)
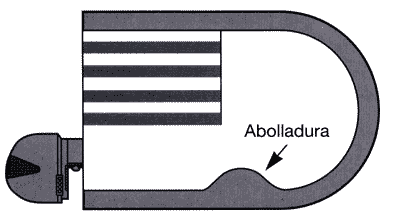
Figura 6.5. Abolladura en la parte posterior de la caldera.
Causa
-
Disminución del espesor de la chapa en esa zona, debido a
condensaciones corrosivas. Por lo general este problema se ve aumentado
por la acumulación de suciedad aparecida como consecuencia de que al
cepillar los tubos, toda la suciedad de los mismos cae al hogar y se va acumulando, formando una incrustación que retiene la humedad y va corroyendo la chapa.
Avería - 6
- Abombamiento de la cámara de combustión en su parte posterior, zona superior o laterales (figura 6.6).
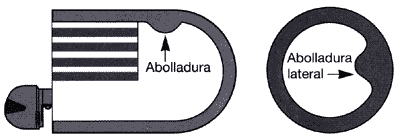
Figura 6.6. Abolladuras en laterales o zona superior.
Causa
- La caldera ha sufrido una sobrepresión por falta de expansión de la instalación debido a:
- Válvulas cerradas.
- Válvulas de seguridad mal reguladas.
- Tubería de seguridad (expansión) dimensionada incorrectamente.
- Membrana deposito expansión cerrado perforada.
- Válvulas de seguridad mal reguladas.
- Tubería de seguridad (expansión) dimensionada incorrectamente.
- Membrana deposito expansión cerrado perforada.
Avería - 7
- Fisura sin/con abombamiento parte antecámara de combustión (figura 6.7).
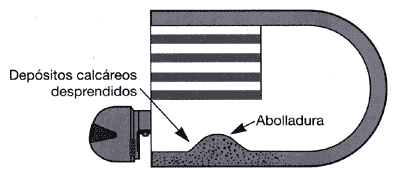
Figura 6.7. Abolladura en antecámara de combustión.
Causa
-
Avería producida por falta de refrigeración de la chapa, debido a
incrustaciones calcáreas desprendidas del haz tubular que se sitúan en
la zona inferior de la caldera.
Avería - 8
- Cámara de combustión completamente deformada (figura 6.8).
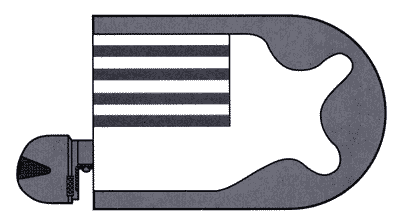
Figura 6.8. Deformación total de la cámara de combustión.
Causa- Normalmente, cuando se produce esta avería es a consecuencia de haberse producido vapor.
Causas de producción de vapor:
- Funcionamiento del circulador a través del termostato Agua Caliente Sanitaria.
- Caldera para calefacción + Agua Caliente Sanitaria.
En verano potencia excesiva de caldera con funcionamiento del circulador a través del termostato Agua Caliente Sanitaria.
CALDERAS DE BAJA TEMPERATURA
CALEFACTAR CUIDANDO EL MEDIO AMBIENTE CON CALDERAS PAROMAT
Directiva Europea 92/42/CEE.
En el año 1992 se publico la directiva europea 92/42/CEE que determine el rendimiento mínimo de las calderas estándar, de baja temperatura y de condensación. Según la citada normativa las calderas de baja temperatura o de condensación obtienen rendimientos muy superiores a los conseguidos por las calderas estándar.
La característica principal de las calderas de baja temperatura es el equipamiento con tubos dobles o triples que permiten modular la temperatura de impulsión en la propia caldera, reduciéndose así las perdidas por radiación y convección en el circuito de caldera (hasta colectores) considerablemente.
El ahorro energético anual en la modernización de instalaciones es de un 20% a un 30% según la antigüedad y el estado de la caldera existente.
En la modernización de calderas de carbón el ahorro puede superar el 50% de las facturas anuales de combustibles.
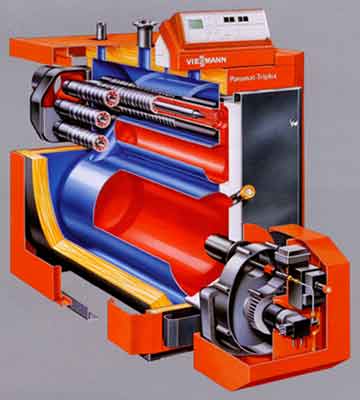
Superficies calefactoras por convección de pared múltiple y triple paso de humos.
EL AHORRO DE ENERGÍA REDUCE LAS EMISIONES DE CO2
Mecanismos de formación de NOx.
A mediados de los años ochenta comenzó a prestarse especial atención a los óxidos de nitrógeno (NOx) al relacionarlos con la "muerte de los bosques". Los NOx se forman como producto de reacciones secundarias en la combustión de los combustibles fósiles.
La formación de óxidos de nitrógeno (NOx ) esta determinada por los siguientes factores:
- La temperatura de la llama: su generación es mínima hasta aproximadamente 1000°C, a partir de 1300° C aumenta su valor de forma progresiva.
- El tiempo de permanencia de los humos en la zona de combustión: cuanto menor sea su permanencia, menor será la cantidad de NOx generado.
- El porcentaje de oxigeno en la zona de reacción: cuanto menor sea el porcentaje de oxigeno, tanto menor será la formación de NOx.
Gracias
al optimo diseño de la caldera y el perfeccionamiento de las técnicas
de combustión, se consiguen reducciones muy importantes en la generación
de NOx.
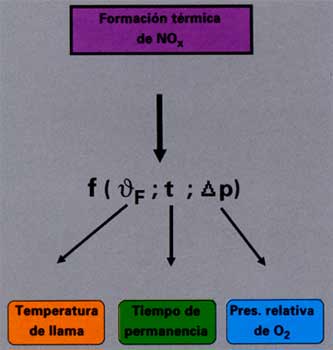
Formación térmica de NO2
Medidas constructivas para la reducción de NOx.
Los
largos años de experiencia acumulados en Viessmann en el desarrollo de
calderas ha permitido que en la serie Paromat-Triplex se haya diseñado
el tamaño y la geometría de la cámara de combustión de forma que no solo
disminuya la temperatura de la llama, sino que simultáneamente se
reduzca el tiempo de permanencia de los humos en la zona de reacción.
Para reducir aun más la formación de NOx,
la caldera Paromat-Triplex-RN dispone de un triple paso de humos. El
segundo y el tercer paso de humos se halla dispuesto sobre el hogar. El
calentamiento homogéneo y la baja carga térmica evitan roturas y
tensiones por dilatación incontrolada de la superficie de intercambio.
Al final de la cámara de combustión (primer paso) los gases de
combustión circulan hacia adelante a través del canal de retorno
(segundo paso), pasando a continuación a los tubos de humos (tercer
paso). Esto permite reducir aun mas el tiempo de permanencia de los
gases de combustión en el hogar.
Reducción de las emisiones de C02 relacionadas con la energía.
Se ha señalado al dióxido de carbono (C02) como el principal causante del efecto invernadero. El C02 es un producto obligado en la combustión de combustibles fósiles. La cantidad de emisiones producidas depende de
la relación hidrogeno/carbono presente en el combustible. En el caso
del lignito, por cada kilovatio-hora generado se producen 0,4 kg de C02; por contra, con el gas natural se generan solo 0,2 kg de C02
por kilovatio-hora. Además de elegir convenientemente el combustible, y
presuponiendo una combustión optima, la forma más eficaz de reducir la
emisión de C02 es consumir menos energía. Aplicado a la técnica de calefacción, esto significa optimizar el rendimiento de las instalaciones.
Las
calderas Paromat-Triplex alcanzan rendimientos estacionales del 95%,
debido a las superficies calefactoras de pared múltiple optimizadas y a
la reducción de las perdidas por disposición del servicio.
Al
modernizar instalaciones de calefacción antiguas (rendimientos
estacionales entre el 70% y el 80%) utilizando una caldera de baja
temperatura Paromat nueva no solo se protege el medio ambiente, sino que
además se reduce considerablemente el consumo de combustible, como muestra convincentemente el ejemplo de más adelante.
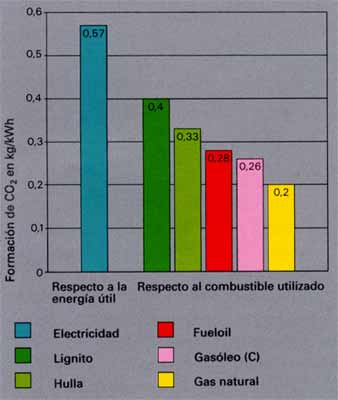
Emisión especifica de C02 de diferentes combustibles energéticos.
Aumento del rendimiento funcionando a baja temperatura
El rendimiento estacional como parámetro de valoración del consumo energético.
El rendimiento estacional de una caldera, según DIN 4702, parte 8 es la magnitud normalizada con la que se expresa analíticamente el rendimiento energético, y por tanto la rentabilidad, de las calderas a lo largo de todo el periodo de calefactación. La definición del rendimiento estacional ofrece la ventaja de que de su valor numérico puede deducirse el consumo de energía de diferentes tipos y modelos de calderas.
Ejemplo
1. Año de construcción de la caldera: 1970Consumo anual de combustible Ca:
Combustible: Gasóleo C
Potencia térmica útil: 105 kW
Modelo/Funcionamiento: Temperatura constante del agua de caldera > 70°C
Rendimiento: h = 80%
Poder calorífico: P.C.I. = 10 kWh/l
Horas de funcionamiento del quemador: hg = 1800 h/a
2. Paromat-Triplex
Año de construcción: 1995Consumo anual de combustible Ba:
Combustible: Gasóleo C
Potencia térmica útil: 105 kW
Modelo/Funcionamiento: Reducción progresiva de la temperatura del agua de caldera.
Rendimiento: hN = 95%
![]()
Este ejemplo demuestra palpablemente que la modernización de la caldera permite ahorrar hasta un 20% de combustible al año, lo cual a su vez redunda en una reducción de la producción de C02
en torno al 20%. Simultáneamente el ejemplo permite ver que el
rendimiento estacional sirve para realizar con facilidad y carácter
general una comparación de los costes energéticos. Considerando este
valor analítico puede determinarse directamente el rendimiento
energético de una caldera y compararlo con el de otros modelos.
Aumento del rendimiento funcionando a baja temperatura con superficies de calefacción de pared múltiple.
Para
aumentar el rendimiento es necesario reducir todas las fuentes de
perdidas. Además de la perdida por humos (una de las principales fuentes
de perdidas de una caldera), el rendimiento se ve influido por las
perdidas por disposición de servicio y las perdidas por radiación y
convección.
Las
perdidas a través del cuerpo de caldera son la suma de las perdidas por
disposición de servicio y las perdidas por radiación y convección que
se producen durante un periodo de calefacción, y dependen del modo de
funcionamiento de la caldera y de la calidad del aislamiento térmico.
Altas perdidas por humos y a través del cuerpo de caldera son
características de las antiguas "calderas a temperatura constante", que,
para evitar la formación de condensados en los tubos de humos deben
funcionar con el agua de caldera a una temperatura mínima de 70°C. Los
rendimientos estacionales de estas calderas son inferiores al 80%: es
decir, se pierde mas del 20% de la energía primaria.
Partiendo
de estos conocimientos, Viessmann ha desarrollado calderas de baja y de
muy baja temperatura, en las que la temperatura del agua de caldera
puede descender progresivamente en función de las condiciones
exteriores. Las de mayor potencia edemas se equipan con quemadores
modulantes de varias etapas, sin el vapor de agua contenido en los humos
se condense en las superficies calefactoras.
Superficies calefactoras de pared múltiple, para lograr gran seguridad de funcionamiento y larga vida útil.
Sobre
todo los tubos de humos deben ser los adecuados para este tipo de
funcionamiento de toma, que con bajas temperaturas del agua de caldera
no se alcanza el punto de rocío del vapor de agua. Este hecho es muy
importante en la fase de arranque. Para evitar eficazmente que en los
tubos de humo se alcance una temperatura inferior al punto de rocío del
vapor de agua, Viessmann desarrollo para las calderas Paromat-Triplex
superficies calefactoras de pared múltiple para el peso dosificado de
calor.
Las
superficies calefactoras de pared múltiple son el resultado de los
esfuerzos de investigación y desarrollo llevados a cabo por Viessmann.
Las superficies calefactoras de pared múltiple
se utilizan desde hace dos décadas y han demostrado fehacientemente una
gran seguridad de funcionamiento y una larga vida útil.
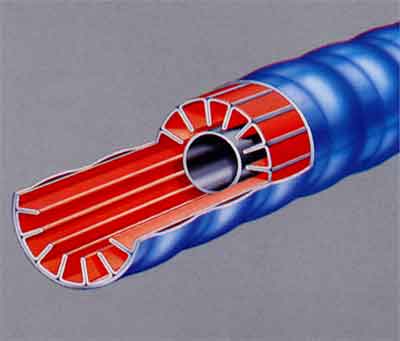
Superficie calefactora de pared múltiple de la caldera Paromat- Triplex.
Superfices calefactoras de pared múltiple: alta seguridad de funcionamiento y larga vida útil
Funcionamiento de los tubos de humos de pared múltiple.
Como en todos los procesos de transmisión de calor, en la transmisión de este desde los gases de combustión a la superficie calefactora y de esta al agua de caldera se opone una determinada resistencia. Este coeficiente de transmisión térmica (coeficiente k) se compone de la suma de las resistencias parciales de los componentes que intervienen, resistencias que dependen del coeficiente de transmisión térmica y de los distintos materiales a tráves de los cuales se transmite el calor.
En función del flujo de la transmisión térmica y de las diferentes inercias térmicas, varián las temperaturas de las superficies calefactoras. En las superficies calefactoras de pared simple, la temperatura superficial del lado en contacto con los humos no viene determinada por la elevada temperatura del gas, sino por la temperatura del agua de caldera mucho mas baja que esta. Por esta razón, el vapor de agua que contienen los humos puede condensar si la temperatura del agua de caldera es inferior a la del punto de roció.
Por el contrario, en las superficies calefactoras de pared múltiple se establece una resistencia a la transmisión térmica. Mediante un diseño adecuado puede optimizarse de tal forma esta resistencia que aun cuando la temperatura del agua de caldera sea inferior a la temperatura del punto de roció, en el lado en contacto con los humos sea siempre superior evitándose la condensación.
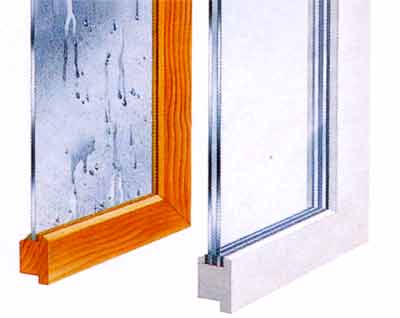
Acristalamiento sencillo - cristales húmedos y empañados, con doble acristalamiento - cristales secos.
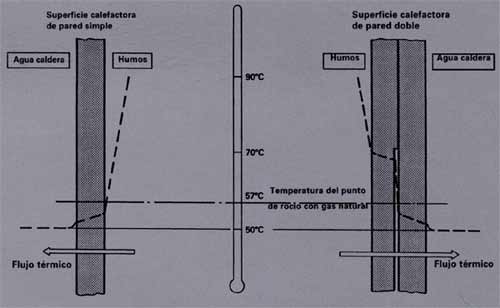
Funcionamiento de las superficies calefactoras de pared simple y pared doble.
Paso dosificado del calor.
Cuando
los gases de combustión recorren los tubos de humos, la temperatura de
los gases de combustión disminuye progresivamente a medida que nos
acercamos a la caja de humos. Esto supone un mayor peligro de que se
alcance el punto de roció en el lado en contacto con los humos. Las
zonas mas expuestas al peligro son aquellas que son recorridas por
humos no muy calientes y que transmiten poco calor al agua de caldera.
En estas zonas la transmisión térmica debe reducirse de forma que la
temperatura superficial este siempre por encima del punto de roció del
vapor de agua. Para ello, en las superficies calefactoras de pared
múltiple el paso del calor se dosifica de manera que se evite la
condensación incluso en la parte trasera de estas.
La
técnologia de la pared méltiple se introdujo en la gama de calderas
medianas y grandes hasta potencias de 5.900 kW. Las superficies
calefactoras de la caldera Paromat-Triplex están compuestas por dos
tubos de acero concéntricos y embutidos uno en otro. Mediante el
prensado del tubo
exterior sobre el interior se obtienen puntos de transmisión térmica
máxima dejando a los lados cámaras de aire que actúan como barreras
térmicas. Variando la distancia de los puntos de prensado se dosifica el
paso del calor (coeficiente k) de manera que se evita que se alcance el
punto de roció.
El tubo
interior esta dotado de unas aletas longitudinales, que logra aumentar
la superficie efectiva de transmisión en el lado en contacto con los
humos con respecto al tubo liso, en aproximadamente dos veces y media.
Por esta razón la Paromat-Triplex necesita menos tubos que las calderas
convencionales. Las superficies calefactoras de pared múltiple
optimizadas permiten rebajar las perdidas por humos hasta valores
inferiores al 7% (en régimen de plena carga) y elevar el rendimiento
estacional al 95%.Amplias cámaras de agua continuas - no se precisa bomba de recirculación
Amplias cámaras de agua.
Una ventaja muy especial de las calderas de chapa de baja temperatura Viessmann son las grandes cámaras de agua que ofrecen una mínima perdida de carga en el lado de humos. La transmisión térmica al agua de caldera se produce por recirculación natural por el efecto termosifón.
Las tomas de impulsión y de retorno están dispuestas en la parte superior de la caldera. Mediante una chapa deflectora el agua de retorno se hace descender hasta la zona media del cuerpo de caldera. Como la temperatura es mas baja que la del agua de caldera que circunda la cámara de combustión, el agua de retorno desciende y desplaza al agua de caldera, mas caliente, de la zona que rodea el hogar. Sobre todo en régimen de carga parcial, el flujo de agua de caldera que recircula por efecto termosifón es mayor que el caudal de agua de retorno. El calor absorbido por las superficies de calefacción puede transmitirse sin obstáculos al agua de caldera. Esto permite, a diferencia de las calderas con reducido volumen de agua, prescindir de una circulación forzada con bomba de recirculación.
Las calderas Paromat no tienden a acumulaciones puntuales de calor, acumulaciones de lodos, ni a la formación de grietas. La disposición optima de la cámara de combustión, el elevado volumen de agua y las amplias cámaras de agua tienen la ventaja adicional de que con quemadores de varias etapas consiguen prolongar los periodos entre arranques del quemador y reducir el numero de arranques. Esto contribuye a reducir las emisiones de contaminantes debidas a los arranques del quemador.

Variación de la temperatura en los tubos de humos de la caldera Paromat-Triplex, y temperaturas del agua de calefacción.
LA CONEXIÓN DE ARRANQUE TRA/TSA sustituye a la bomba de anticondensaciÓn y REDUCE EL TIEMPO DE INSTALACIÓN
La regulación TRA/TSA sustituye a la bomba de anticondensación y ahorra tiempo de montaje.
Gracias
a las especiales características de la superficie de calefacción de
pared múltiple, las calderas de baja temperatura Paromat pueden
funcionar con temperaturas de retorno mínimas de 30°C si utilizan
gasóleo, o de 40°C si utilizan gas. El desarrollo de la conexión de
arranque "TSA" de Viessmann y el diseño descrito anteriormente de
"amplias cámaras de agua", hace innecesaria la bomba de
anticondensación para elevar la temperatura de retorno en las calderas
Paromat hasta 460 kW. Esto simplifica la conexión hidráulica de los
circuitos de calefacción correspondientes y reduce los costes de
instalación.
Aplicación de la conexión de arranque TRA/TSA
La
conexión de arranque TRA/TSA se aplica en calderas de 80 a 460 kW.
Con la regulación Trimatik se utiliza el termostato TRA, mientras que
con la Dekamatik M1, M2, E y KR se aplica la sonda TSA.
La Dekamatik HK actúa asimismo a través del Bus de dos hilos, estrangulando el paso de agua.
Cuando
se utilice la regulación KR debe actuarse sobre válvula mezcladora o
bombas de calefacción a través de una conexión a realizar in situ. La
sonda de temperatura mide la temperatura de la mezcla del agua de
retorno y del agua de caldera. Cuando la temperatura de caldera es
inferior a la prefijada en fabrica, la regulación
Dekamatik-DE o Dekamatik-HK accionan las válvulas mezcladoras de
determinados circuitos de calefacción, estrangulando al menos en un
50% el caudal de retorno. El gran volumen de agua, las amplias cámaras
de agua y la buena recirculación natural que se consigue,
proporcionan un calentamiento uniforme y evitan la formación de
condensados. Cuando se alcanza la temperatura ajustada en fabrica se
desbloquean de nuevo los circuitos de calefacción estrangulados.
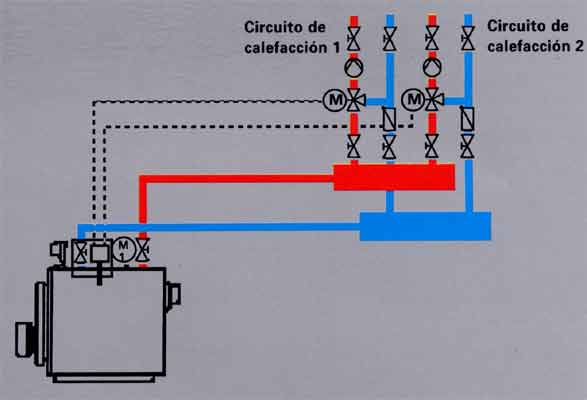
En
la fase de arranque, la conexión de arranque TRA/TSA actúa sobre las
válvulas mezcladoras de los circuitos de calefacción. El caudal de
agua que atraviesa la caldera se reduce al menos un 50%.
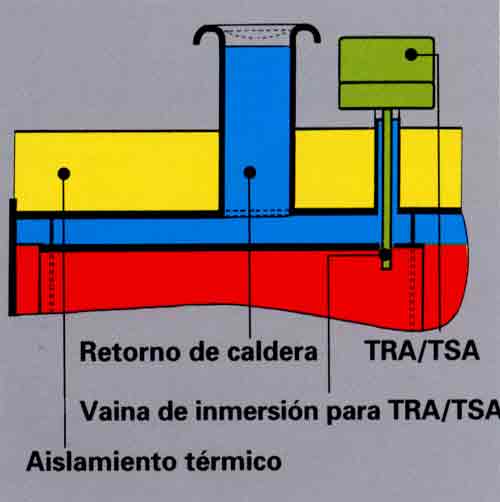
La conexión de arranque TRA/TSA permite prescindir de la elevación de la temperatura de retorno.
DIMENSIONADO DE CENTRALES TÉRMICAS PARA CALEFACCIÓN Y A.C.S. CON CALDERAS DE BAJA TEMPERATURA Y CONDENSACIÓN
CRITERIOS
DE DIMENSIONAMIENTO DE CENTRALES TÉRMICAS PARA CALEFACCIÓN Y
PREPARACIÓN DE ACS CON GENERADORES DE CALOR DE BAJA TEMPERATURA Y DE
CONDENSACIÓN
ANTECEDENTES
Se
parte de los datos de dimensionamiento de los sistemas centralizados de
preparación de agua caliente para usos sanitarios en edificios de
viviendas, indicados en el DTIE 1.01 de ATECYR.
La
vivienda denominada «estándar» en el DTIE esta constituida por un
cuarto de bario completo y una cocina. Se puede suponer que la
superficie de esta vivienda sea de 50 a 60 m2 y que la potencia de calefacción, dependiendo de la zona climática, este comprendida entre 4 y 8 kW (70 a 160 W/m2).
Además,
por las razones indicadas en el citado DTIE, se asume que el ACS sea
preparada a una temperatura comprendida entre 50°-y 55° C.
En lo que sigue se aplicara la siguiente simbología:
PACS potencia máxima demandada por el servicio de agua caliente sanitaria.
PCAL potencia máxima demandada por el servicio de calefacción.
P
PCEN potencia de la central, articulada sobre una o mas calderas![]()
![]()
![]()
PGEN potencia de un generador de calor.
f factor de aumento por puesta a régimen y selección del tamaño de caldera disponible en el mercado.
La relación r
arriba definida es variable, dependiendo, aparte del tipo de sistema de
acumulación, del numero de viviendas; disminuye de forma asintótica al
aumentar el numero de viviendas por el efecto de la simultaneidad de
funcionamiento de los aparatos sanitarios, según se indica
cualitativamente en el grafico de la figura 1.
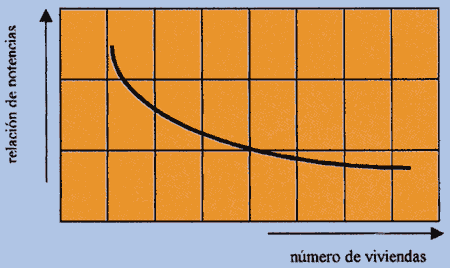
Considerando
el factor de aumento f, que suele estar entre el 8% y el 15% de la
potencia de calculo, la potencia de la central PCEN es:
Queda
disponible, por tanto, un cierto margen durante el periodo de demanda
máxima, que suele considerarse de seguridad y que, mas adelante, se
aprovechara para conseguir el propósito que se persigue.
La
idea que se expresa a continuación nace de la aplicación de las
calderas mixtas, con o sin deposito acumulador, en instalaciones
individuales de calefacción y agua caliente sanitaria destinadas a
viviendas. En estos casos, cuando existe demanda de ACS la potencia de
estas calderas viene totalmente dedicada a este servicio. El sistema de
calefacción queda sin suministro de potencia durante un tiempo que
depende de la duración de la demanda de ACS. La inercia de los locales
permite que la temperatura en las habitaciones quede prácticamente
constante.
Los criterios de diseño de estas instalaciones quedan analíticamente expuestos con estas relaciones:
si PCAL > PACS entonces PGEN = PCAL
Si PCAL < PACS entonces PGEN = PACS
La segunda proposición es la más común en instalaciones individuales sin acumulación. Se trata de extender parcialmente este criterio a los sistemas centralizados de
preparación de ACS para viviendas, del tipo con acumulación o con
semi-acumulacion (o semi-instantaneos), en los que la potencia para ACS
es casi siempre inferior, si no muy inferior, a la de calefacción, sin
que se resientan las temperaturas de los locales calefactados.
El croquis de la figura 2 representa la idea en términos de potencia.
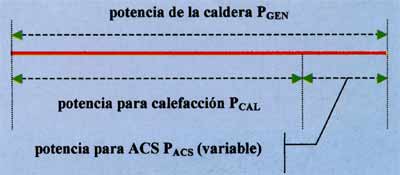
En otras palabras, se trata de establecer un coeficiente ß, mayor que 1, tal que:
PGEN = ß x PCAL £ (1 + r) x PCAL = c x PCAL = PCAL + PACS = P
Se hace hincapié en que esta proposición es valida sola mente
para calderas de baja temperatura y de condensación, cuyo rendimiento
aumenta al disminuir la demanda por permitir una notable disminución del
nivel térmico del agua y, sobre todo, por sus bajas perdidas por
disponibilidad; no es recomendable, por tanto, para calderas
convencionales, aunque sea conceptualmente aplicable.
El fin último es el de ahorrar en los costos de inversión y de explotación.
SISTEMAS DE SEMIACUMULACIÓN
Para estos sistemas, definidos para un tiempo de preparación de 10 minutos, la relación r esta comprendida entre 0,3 y 1,5, en cifras redondas.
La reducción del servicio de calefacción durante el periodo de punta de ACS es admisible siempre que este no coincida
con la demanda máxima de calefacción. Se menciona que durante el
periodo de punta de ACS pueden darse puntas sucesivas de 10 minutos
(entre 4 y 10, dependiendo del numero de viviendas servidas por el
sistema, aunque de intensidad algo diferente).
Se propone que el coeficiente ß antes definido se calcule de acuerdo a las siguientes ecuaciones, en función, precisamente, de la relación r de potencia de los dos servicios (tabla 1).
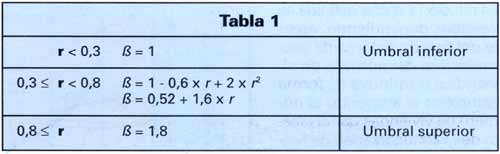
Estas ecuaciones están representadas en la figura 3:
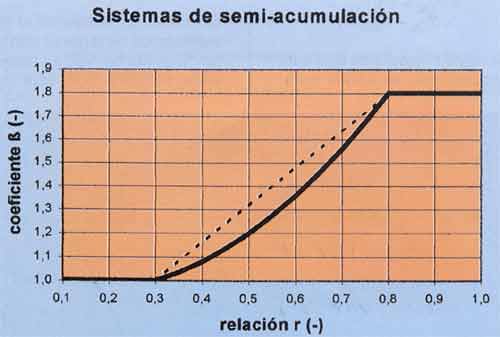
Para valores de r
entre 0,3 y 0,8 se proponen dos ecuaciones, una cuadrática y otra
lineal, algo mas conservadora. En edificios de viviendas suelen darse
tres puntas diarias. La primera de ellas es a primeras horas de las
mañanas y es de intensidad mediana; el sistema de calefacción suele
estar parado y los depósitos están cargados. La segunda se da a
mediodía; la punta es relativamente pequeña y no presenta problema
alguno desde el punto de vista aquí tratado, ya que la potencia
demandada por el servicio de calefacción esta cerca del mínimo,
probablemente. La tercera y mas importante se da a ultimas horas de las
tardes; en estos momentos la demanda de calefacción es inferior a la
máxima porque las condiciones exteriores no son extremas, salvo días
excepcionalmente fríos y porque las ganancias interiores de calor por
personas, alumbrado y aparatos son máximas.
Queda, por tanto, una potencia disponible para el servicio de ACS debida a estos tres factores:
1. El exceso de potencia con el que se ha dimensionado la caldera (factor f).2. El exceso de potencia por menor demanda del servicio de calefacción.3. La potencia que el servicio de ACS quitara temporalmente al servicio de calefacción.
Ejemplo.
Se
supone un edificio de 30 viviendas, cada una con una potencia de
calefacción de 7 kW. Según el Anexo al DTIE 01.1 (ATECYR), el sistema de
preparación por semi-acumulacion de ACS a 55° C necesita una potencia
de 98 kW, con un volumen de acumulación de 489 litros.
Por tanto, resulta:
potencia necesaria para calefacción
30 x 7 210 kW
potencia necesaria
para ACS 98 kW
para ACS 98 kW
potencia total 308 kW
El coeficiente ß resulta ser:
ß = 1-0,6 x r + 2 x r2 = 1 - 0,6 x 0,47 + 2 x 0,472 = 1,16ß2 = 0,52 + 1,6 x r = 0,52 + 1,6 x 0,47 = 1,27
y, por tanto, los posibles valores de la potencia térmica de la caldera son:
PGEN,1 = 1,16 x 210 = 244 kWPGEN,2 = 1,27 x 210 = 267 kW
En los dos casos, durante una punta de máxima potencia del ACS quedan disponibles para el servicio de calefacción:
PCAL,1 = 2,44 - 98 = 146 kWEn ambos casos, la potencia disponible para el servicio de calefacción cubre sobradamente la demanda en casi todos los casos o, cuando así no sea, el efecto producido será muy leve, porque la inercia térmica del edificio mantendrá la temperatura de los locales prácticamente constante.
(70% de la demanda máxima)
PCAL,2 = 2,67 - 98 = 169 kW
(80% de la demanda máxima)
Se
elige una caldera Paromat Triplex de 285 kW de potencia útil, que cubre
las necesidades para el caso más conservador (la caldera inferior es de
225 kW y seria insuficiente) y satisface, en el peor de los casos, la
demanda de calefacción al 89%.
Para
el caso del verano, la relación PACS/PGEN resulta igual a 98/285=0,34 y
es muy satisfactoria en cuanto a posibilidades de regulación.
Resumiendo,
el grado de cobertura, definido como relación entre potencia máxima
demandada y potencia del generador, de la caldera seleccionada es, para
los tres casos extremos:
solo calefacción: 285/210 =1,36calefacción y ACS: 285/(210+98) =0,93solo ACS: 285/98 =2,91
SISTEMAS DE ACUMULACIÓN
Para estos sistemas, que, normalmente, se dimensionan con 2 horas de tiempo de recuperación, la relación r esta comprendida entre 0,1 y 0,4.
Con
estos sistemas no se puede, obviamente, aplicar el mismo criterio,
debido a que el sistema de calefacción quedaría sin servicio durante un
periodo de tiempo bastante grande. La reducción en la potencia total de
la caldera deberá ser inferior.
Se proponen las relaciones expuestas en la tabla 2. y que se representan en la figura 4.
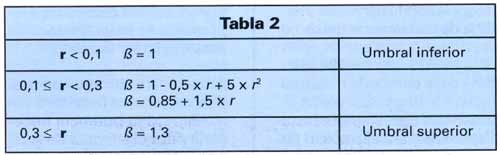
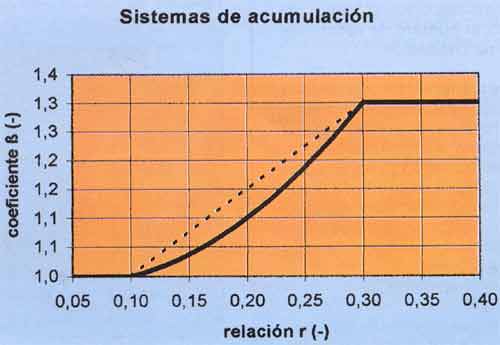
También ahora se proponen dos relaciones para valores de r entre 0,1 y 0,3, una cuadrática y la otra lineal.
Es evidente que con el sistema de acumulación las ventajas que se logran son menores que con el sistema de semi-acumulacion.
Además, se debe comprobar que durante el verano la parcialización del quemador permite trabajar con demandas muy pequeñas.
Ejemplo.
Siguiendo con el ejemplo anterior, se dimensiona un sistema de acumulación con 2 horas de preparación.
Según
el citado Anexo al DTIE 01.1, el sistema de preparación por acumulación
de agua a 55° C necesita de una potencia de 29,7 kW, con un volumen de
acumulación de 2.851 litros.
Por tanto, resulta:
potencia necesaria para calefacción30 x 7 210,0 kW
potencia necesaria
para ACS 29,7 kW
potencia total 239,7 kW
![]()
El coeficiente ß resulta ser:
ß1 = 1 - 0,5 x r + 5 x r2 = 1 - 0,5 x 0,14 + 5 x 0,142 = 1,028ß2 = 0,85 + 1,5 x r = 0,85 + 1,5 x 0,14 = 1,06
y, por tanto, los posibles valores de la potencia térmica de la caldera son:
PGEN,1 = 1,028 x 210 = 216 kWPGEN,2 = 1,06 x 210 = 223 kW
y durante una punta de máxima potencia del ACS quedan disponibles para el servicio de calefacción:
PCAL,1 = 216 - 29,7 = 186 kW
(89% de la demanda máxima)PCAL,2 = 223 - 29,7 = 197 kW
(94% de la demanda máxima)
En ambos casos, la potencia disponible para el servicio de calefacción cubre sobradamente la demanda en todos los casos.
La
caldera Paromat Triplex de 225 kW de potencia útil cubre las
necesidades para ambos casos (la caldera inferior, de 170 kW, séria
insuficiente).
Para el caso del verano, la relaci6n PACS/PGEN
resulta igual a 29,7 / 225 = 0,13 y es todavía satisfactoria en cuanto a
posibilidades de regulación, siempre que se instale un quemador de dos
marches o modulante.
Resumiendo, el grado de cobertura antes definido de la caldera seleccionada es:
sólo calefacción: 225 / 210 =1,07calefacción y ACS: 225 / (210 + 29,7) = 0,94sólo ACS: 225 / 29,7 = 7,58
NÚMERO DE GENERADORES
Queda
ahora por determinar el numero de calderas con el que satisfacer la
demanda total asó calculada o, mejor dicho, el numero de escalones de
parcialización.
Las
calderas que son objeto de este estudio (de baja temperatura y de
condensación) ofrecen las mejores prestaciones cuando trabajan a carga
parcial, sobre todo si los sistemas están diseñados pare este tipo de
calderas y que el control sea adecuado al fin que se persigue, como se
vera mas adelante.
Desde
este punto de vista, por tanto, e independientemente de los
requerimientos del Reglamento, una sola caldera representa la solución
idónea para cualquier potencia.
En
verano y durante las medias estaciones la caldera suministrara la
potencia necesaria para el servicio de ACS trabajando siempre a carga
parcial, con rendimiento elevado. Es suficiente asegurar que el factor
de carga sea igual o superior a 0,1 con una caldera de baja temperatura y
a 0,05 con una de condensación.
El factor de carga fc se define como la relación anual entre las horas en las que el quemador-suministra calor a la instalación hu (horas útiles) y las horas totales de funcionamiento ht:
La figura 5 expresa gráficamente estos conceptos (el tiempo esta en ordenadas).
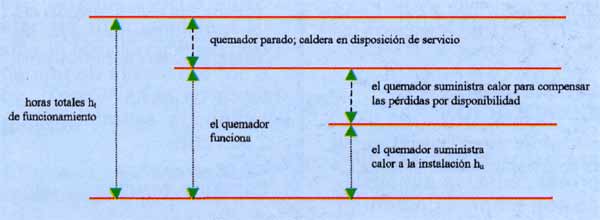
La figura 6 indica el rendimiento medio estacional en función del factor de carga fc
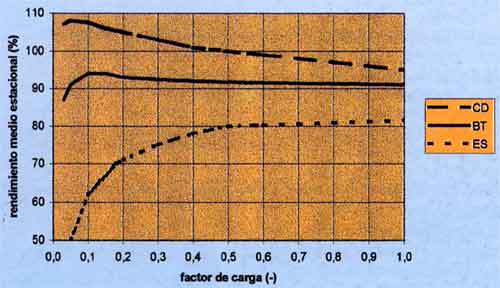
Nota: CD: ConDensación; BT.- Baja Temperatura; ES. Estándar. Figura 6.
Considerando
que el factor de carga medio estacional de una central que da servicio
de calefacción y agua caliente sanitaria puede estar alrededor del 30%,
resulta que, con respecto al rendimiento a plena carga, el rendimiento
medio estacional baja unos 7 puntos en una caldera estándar mientras que
aumenta de 1 a 2 puntos en una caldera de baja temperatura y de 8 a 9
puntos en una caldera de condensación.
Por
contra, existen razones de fiabilidad de la central de producción de
calor que cada técnico considera de forma diferente. Los parámetros que
pueden entrar en juego son muchos, empezando por el use del edificio y
terminando por la calidad de las calderas. Es conveniente que las
calderas que se vayan a instalar en paralelo sean de igual tamaño pare
un mejor equilibrado hidráulico
de la central y para una cuestión de repuestos. Incluso en caso de
grandes centrales, articuladas sobre 3 o mas generadores, deberá
pensarse en una división con tamaños iguales. Una vez mas, estas
consideraciones no son validas para calderas convencionales.
Seria
conveniente también que la caldera que vaya a actuar como base sea del
tipo de condensación o de baja temperatura con recuperador del calor de
los humos, siempre que el sistema de calefacción este diseñado para
ello.
CONTROL
La
cuestión de los escalones de parcialización o la adopción de quemadores
modulantes afecta a la frecuencia de arrancadas de cada generador y,
por tanto, a su rendimiento medio estacional.
Una recomendación podriá ser la siguiente:
- hasta 70 kW: 1 marcha; todo-nada- de 70 a 400 kW: 2 marchas; todo-poco-nada- mas de 400 kW modulante.
Sin
embargo, en caso de adoptar una sola caldera para ambos servicios, no
es recomendable instalar quemadores de una sola marcha e, incluso,
conviene pensar en los modulantes para potencias inferiores a la
indicada arriba.
Por ultimo, debe hacerse una consideración sobre el control de la central.
Considerando
que el agua caliente sanitaria debe prepararse a una temperatura entre
50° y 55° C, el agua en salida de la central deberá tener una
temperatura mínima de 65° - 70° C, dependiendo de la superficie del
intercambiador de calor.
Por
otro lado, el sistema de calefacción, que se suele dimensionar para
temperaturas de 80° C y superiores, puede y debe necesitar temperaturas
mas bajas, sobre todo si esta a servicio de sistemas de calefacción por
suelo radiante, hasta el limite admitido en los generadores de baja
temperatura para evitar condensaciones (unos 35° C a 40° C en calderas
de baja temperatura alimentadas con gas natural).
Por
tanto, deberá existir un dispositivo automático que aumente el nivel
térmico de funcionamiento de la caldera cuando el agua caliente
sanitaria demande servicio, enclavado con la bomba de circulación del
agua del intercambiador.
El esquema de una central articulada sobre un solo generador, sin bomba primaria, esta dibujado en la figura 7.
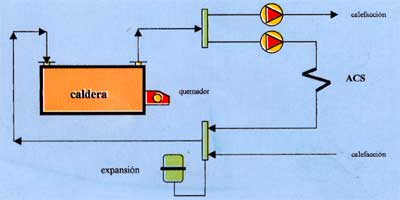
Cada
circuito de calefacción deberá estar dotado de una válvula de tres vías
para variar la temperatura del agua en función de las condiciones
exteriores. Esta válvula deberá recibir una señal imperativa de parte
del lazo de control del circuito de ACS que limite la abertura de la
misma a un valor máximo cuando exista demanda.
Este valor máximo podrá ser fijo, con lo cual se corre el riesgo de reducir innecesariamente la potencia disponible para el servicio de calefacción, o variable con la demanda de ACS, lo que complica un poco el sistema de control.
Si
existe solamente un circuito de calefacción la instalación de una
válvula de tres vías no es necesaria, ya que la caldera de baja
temperatura admite temperaturas de retorno del sistema de unos 40° C,
como se ha dicho. Tampoco se necesita la bomba primaria, ya que estas
calderas tienen una circulación natural interior asegurada por su gran
volumen de agua.
Se
debe tener presente que la demanda del sistema de ACS, aún cuando sea
con acumulación, es variable con la diferencia media logarítmica de
temperatura entre el agua del circuito primario y el agua sanitaria.
El
régimen transitorio al que esta sometido el intercambiador de calor
permite modular la señal imperativa a la que se hacia referencia arriba.
Para ello es necesario medir la potencia en cada instante demandada por
el servicio de ACS y actuar en función de ella.
Para la
medida de la potencia demandada por el acumulador se deben conocer tanto
el caudal de agua primario como el diferencial de temperatura entre
entrada y salida. El primero se puede medir directamente mediante
costosos dispositivos o, alternativamente, se puede recurrir a la medida
indirecta a través de la curva característica de la bomba, debidamente
garantizada por el fabricante. La medida de temperatura no presenta
ninguna dificultad.
El esquema de la figura 8 presenta los aparatos de control necesarios, aparte el control de la caldera.
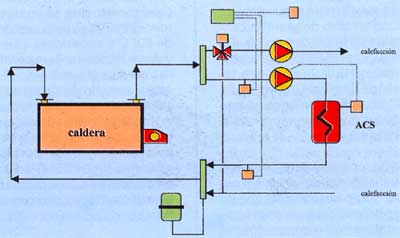
Se
observa que el control sobre el circuito de ACS se hace actuando
directamente sobre la bomba de circulación en manera todo-nada. Este
tipo de control es apto solamente para sistemas de semi-acumulacion.
Para
sistemas de acumulación conviene instalar una válvula de tres vías
sobre el circuito primario de agua del intercambiador, exterior a los
depósitos, como se indica en el esquema de la figura 9.
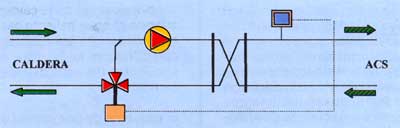
Ahora
la válvula podrá enviar una señal imperativa a las válvulas de los
circuitos de calefacción que sea proporcional a su abertura.
6. CONCLUSIONES
En conclusión, puede afirmarse que la combinación en una sola caldera de baja temperatura o condensación de
los servicios de calefacción y agua sanitaria es viable y permite unos
ahorros importantes tanto en costo de inversión como de explotación.
TÉCNICA DE CONDENSACIÓN EN CALDERAS
Con el desarrollo de la técnica de condensación, la industria de la calefacción avanzo un paso mas hacia la consecución de un aprovechamiento máximo del combustible. La técnica de condensación ofrece la posibilidad de reducir drásticamente el consumo de gas, tanto en pisos y en casas unifamiliares, como en edificios de oficinas, comerciales, industriales y públicos.
La gran cantidad de calor contenido en los humos que en las "calderas convencionales" a través de la chimenea puede aprovecharse con la técnica de condensación. Esta tecnología se distingue por sus mínimas emisiones de contaminantes y un funcionamiento excepcionalmente rentable de la instalación.
Acuciados por la necesidad de buscar nuevas soluciones para una utilización más racional y sensata de las fuentes de energía no renovables, como el carbón, el petróleo y el gas natural, en los últimos anos la industria y la ciencia se han visto forzadas a desarrollar nuevas tecnologías.
Además del factor económico, la protección del medio ambiente ha pasado en gran medida a un primer plano.
El principio básico es que un menor consumo de energía unido a un mejor aprovechamiento de la misma, conlleva a una reducción de las emisiones contaminantes.
Calor procedente de los humos.
Un avance importante en este sentido fue la introducción de las calderas de baja y muy baja temperatura. Un funcionamiento adaptado a las necesidades caloríficas permitió reducir las perdidas y aumentar el rendimiento estacional hasta alcanzar el 94%.
Con la técnica de condensación se reduce considerablemente el calor residual que pierden los humos en la chimenea. Adicionalmente, la condensación del vapor de agua permite aprovechar también el calor latente contenido en los humos.
¿Que sucede durante la combustión?
Durante la combustión los componentes combustibles de los carburantes, fundamentalmente carbono (C) e hidrogeno (H), reaccionan con el oxigeno del aire, formando dióxido de carbono (C02), vapor de agua (H20) y calor. El ejemplo de la formula de la combustión del metano (CH4), que constituye cerca del 90% del gas natural, lo muestra claramente:
CH4 + 202 ® C02 + 2H2OEl calor latente (también denominado calor de condensación) contenido en los humos, es liberado en la condensación del vapor de agua generado durante la combustión y transferido al agua de caldera. En el caso de utilización de gas natural, el rendimiento estacional puede aumentarse hasta un 15% en relación a una caldera de baja temperatura. La consecuencia es que el consumo de energía necesario para generar la cantidad de calor deseada es considerablemente menor. La ilustración adjunta muestra el esquema de flujos térmicos correspondientes a una caldera de baja o muy baja temperatura y una caldera de condensación. Técnica de condensación.
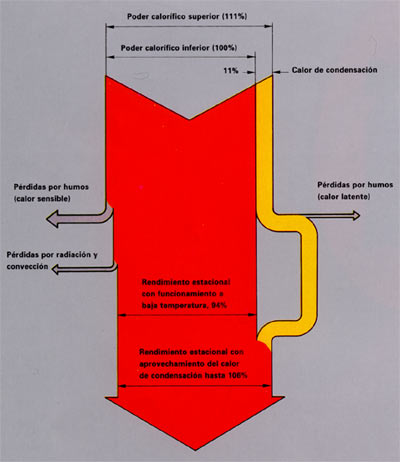
Esquema de flujos térmicos.
Poder calorífico superior y poder calorífico inferior
Poder energético de los combustibles.
La cantidad de calor liberada en la combustión completa, se denomina poder calorífico. En los combustibles cuyos humos contienen vapor de agua se distingue entre el poder calorífico inferior (P.C.I.) y el poder calorífico superior (P.C.S.).
Poder calorífico superior y poder calorífico inferior.
Se denomina poder calorífico inferior (P.C.I.) a la cantidad de calor que se libera en una combustión completa cuando el agua originada esta presente en forma de vapor.
El poder calorífico superior (P.C.S.) es la cantidad de calor liberada en la combustión completa, incluido el calor de condensación del vapor de agua contenido en los humos.
En las calderas convencionales no puede producirse la condensación de los gases de combustión, pues ello produciría danos por corrosión en las superficies de calefacción. Por esta razón, hasta ahora no era posible aprovechar el calor de condensación. Por ello, en los cálculos del rendimiento siempre se utiliza como magnitud de referencia el poder calorífico inferior (P.C.I.). El aprovechamiento adicional del calor de condensación permite que se de el hecho curioso de que pueda obtenerse un rendimiento estacional superior al 100%.
Para poder comparar las calderas convencionales con las de condensación, los rendimientos estacionales de ambas deben seguir refiriéndose al poder calorífico inferior (P.C.I.).
Las
tablas adjuntas muestran la relación existente entre el poder
calorífico superior (P.C.S.) y el poder calorífico inferior (P.C.I.) en
los diferentes combustibles.
En
general puede decirse que cuanto mayor es la diferencia entre el poder
calorífico superior (P.C.S.) y el poder calorífico inferior (P.C.I.),
mayor es el aprovechamiento que se puede obtener aplicando la técnica de
condensación.
En
el caso del gasóleo la diferencia entre el poder calorífico inferior y
el superior es del 6%, y en el caso del gas natural del 11%; es decir,
el aprovechamiento de la condensación es particularmente elevado en el
caso del gas natural.
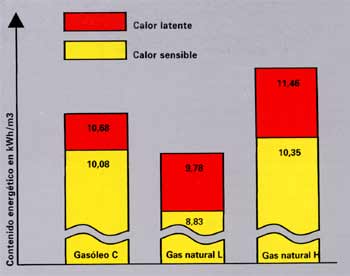
Contenidos energéticos del gasóleo C y del gas natural.
La técnica de condensación aprovecha las ventajas del gas natural.
La
utilización de gas natural tiene otras ventajas adicionales, que pueden
aprovecharse con la técnica de condensación para generar calor de forma
particularmente rentable y ecológica.
• El gas natural tiene un mayor contenido de hidrogeno que el gasóleo C, por lo que sus humos tienen un mayor contenido de vapor de agua. Por consiguiente, el calor obtenido por condensación es mayor que en el del gasóleo.• La temperatura del punto de rocío del gas natural es 10K superior a la temperatura del punto de rocío del gasóleo C. Esto implica un mayor aprovechamiento energético en cada temporada de calefacción.• Al contrario que el gasóleo C, en la combustión del gas natural no se producen óxidos de azufre (S02/SO3), que podrían unirse con el agua condensada dando lugar a ácido sulfúrico.
Poder calorífico superior (P.C.S.) (kWh/m3) | Poder calorífico inferior (P.C.I.) (kWh/m3) | HO/HU | HO-HU (kWh/m3) |
Cantidad de condensados (teórica) (Kg/m3) 1) | |
Gas ciudad | 5,48 | 4,87 | 1,13 | 0,61 | 0,89 |
Gas natural H | 11,46 | 10,35 | 1,11 | 1,11 | 1,63 |
Propano | 28,02 | 25,80 | 1,09 | 2,22 | 3,37 |
Butano | 37,19 | 34,35 | 1,08 | 2,84 | 4,29 |
Gasóleo C 2) | 10,68 | 10,08 | 1,06 | 0,60 | 0,88 |
|
Contenidos energéticos de los diferentes combustibles.
Factores que influyen en el aprovechamiento optimo de la técnica de condensación
Influencia del sistema de calefacción.
La cantidad de agua condensada que puede conseguirse mediante el calor de condensación asociado, dependen de ciertos factores. Además de la influencia que ejercen el tipo de combustible, la temperatura y humedad del aire de combustión, y el exceso de aire, desempeña un papel primordial la temperatura del sistema de calefacción.
El rendimiento de la técnica de condensación se aprovecha íntegramente en los sistemas de calefacción con reducidas temperaturas de retorno, puesto que esta circunstancia permite extraer mas cantidad de calor de los humos. En un sistema diseñado con una temperatura de impulsión de 40°C y una temperatura de retorno de 30°C (p.ej., en suelos radiantes o en sistemas de calefacción de diseño similar), se consigue un elevado aprovechamiento de la energía. No obstante, en los sistemas diseñados p.ej., con temperaturas de 90/70°C, también aumentan considerablemente los rendimientos gracias al funcionamiento en descenso progresivo de la temperatura del agua de caldera, en función de la temperatura exterior. Necesidad de un reducido exceso de aire.
La influencia que el exceso de aire tiene en la combustión no puede despreciarse, puesto que el punto de rocío del vapor de agua depende del mismo, y consecuentemente del contenido de C02 de los humos. Cuanto menor sea el exceso de aire (es decir, cuanto mayor sea el contenido de C02), mayor será el punto de rocío del vapor de agua, y por tanto, mayor el aprovechamiento de la técnica de condensación.
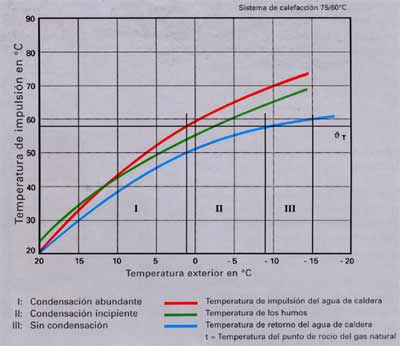
Influencia de la temperatura del sistema de calefacción en calderas de condensación a gas.
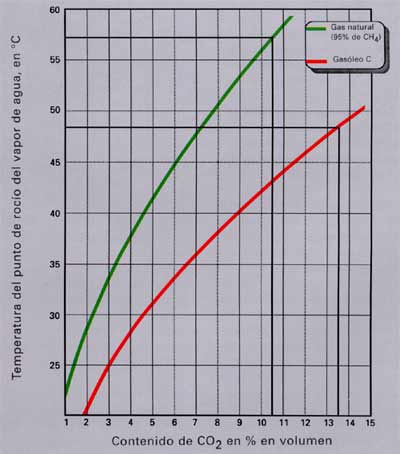
Temperatura del punto de rocío del vapor de agua.
Elevada seguridad de funcionamiento y larga vida útil gracias a las superficies calefactoras Inox-Crossal
Acero inoxidable especial para una elevada seguridad de funcionamiento y larga vida útil.
Las calderas de condensación Viessmann disponen de superficies calefactoras Inox-Crossal fabricadas en acero especial de alta aleación (aleación cromo-níquel-molibdeno estabilizada al titanio) resistente a la corrosión.
El acero inoxidable especial resiste los condensados ácidos y ofrece elevada seguridad de funcionamiento y gran longevidad.
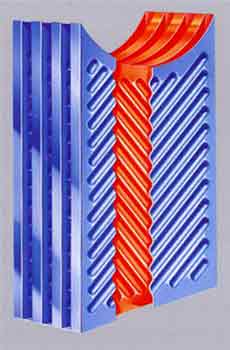
Superficies
calefactoras Inox-Crossal de acero inoxidable especial para una elevada
seguridad de funcionamiento y larga vida útil.
Rendimiento de hasta el 109%.
Las
superficies calefactoras InoxCrossal son superficies intercambiadoras
de calor de alto rendimiento que fomentan la condensación mediante un
sistema de contraprensádos que producen una gran turbulencia en los
humos.
Esto
permite que todas las moléculas de los humos entren en contacto con la
superficie de intercambio. La temperatura de esta es, en función de la
temperatura de retorno, inferior a la del punto de rocío del vapor de
agua (58°C), por lo tanto el vapor de agua sufre una condensación
intensa en las superficies calefactoras, transfiriendo el calor liberado
al agua de caldera como energía calorífica adicional.
Las
superficies Inox-Crossal transmiten el calor al agua de caldera con una
elevadísima eficacia: esto permite que la temperatura de los humos sea
entre 5 y 15K superior a la temperatura de retorno, por lo que las
perdidas por humos son extremadamente reducidas en todo el periodo de
calefacción y en cualquier condición de funcionamiento. La intensa
condensación y ]as bajas temperaturas de los humos consiguen
rendimientos de hasta el 109% (referidos al poder calorífico inferior
del gas natural) en función de la temperatura del sistema.
Incluso
en un sistema de distribución térmica convencional diseñado para
temperaturas de 90/70°C el rendimiento puede llegar al 106%. Durante la
producción del 90% de la energía anual necesaria para calefacción se
aprovecha total o parcialmente el poder calorífico superior. Las
calderas de condensación Viessmann no sólo consiguen rendimientos
excepcionales con sistemas de calefacción diseñados con bajas
temperaturas (p.ej., suelo radiante); también puede hacerlo con emisores
convencionales (radiadores).
Superficies calefactoras Inox-Crossal de disposición vertical.
Las
superficies de calefacción InoxCrossal están dispuestas verticalmente:
es decir, el agua condensada producida fluye de arriba hacia abajo sin
ningún obstáculo y en el mismo sentido que los humos, así se evitan las
concentraciones ácidas debidas a la revaporización del agua condensada.
El agua condensada que se forma lava las superficies de intercambio
manteniéndolas permanentemente limpias.
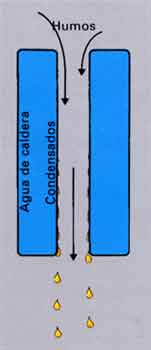
Requisitos físicos necesarios en la conducción de los humos y de los condensados.
Necesidad del conducto de humos. Debido a la reducida temperatura de los humos y al pequeño tiro que ello conlleva, y teniendo en cuenta la continua condensación de los humos de evacuación, no puede utilizarse una chimenea convencional en la técnica de condensación. Por tanto, para instalar una caldera de condensación hay que disponer de conductos de humos de acero inoxidable.
Para las calderas Vertomat la chimenea podrá ser de acero inoxidable con pared simple, es decir, sin aislamiento térmico.
Por ser la temperatura máxima de los humos de las calderas de condensación de unos 80°°-C se comprende que existe también la posibilidad de utilizar materiales plásticos, siempre que sean resistentes a esa temperatura y a la acción de los condensados.
En el mercado existen materiales de este tipo, como el propileno, que resiste temperaturas de hasta 120°°-C y el RV.D.F. que resiste hasta 160°°-C.
Para la caldera Eurola, Viessmann proporciona sistemas de evacuación de humos estancos resistentes a la corrosión; los sistemas están verificados y homologados. En concreto, los sistemas pueden instalarse:
• a lo largo de chimeneas o canales ventilados (p.ej., chimeneas domesticas);• en pasos verticales del plano de cubierta (p.ej., chimenea de mocheta) en caso de instalación en cubierta;
•
para evacuar a través de pared exterior: pasamuros exterior. Será
siempre necesario consultar la reglamentación local para la ejecución de
conductos de humos.
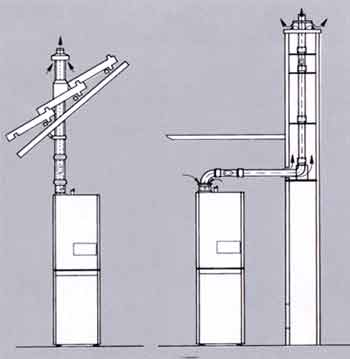
Conductos de humos la caldera de condensación a gas Eurola.
Evacuación a la red publica de alcantarillado.
Los condensados producidos en la combustión y durante el enfriamiento de los humos deben evacuarse adecuadamente.
- Las autoridades locales pueden exigir evacuar el agua de condensación sometiéndola a una neutralización previa.
Como
es natural, la tubería de evacuación de condensados entre la caldera de
condensación y el sistema domestico de evacuación de aguas residuales
debe estar formada por un material resistente a la acción de los
condensados. Para los cados en que la autoridad local competente exija
la neutralización del agua condensada, Viessmann ofrece para cada
caldera de condensación a gas el equipo de neutralización adecuado,
listo para conectar.
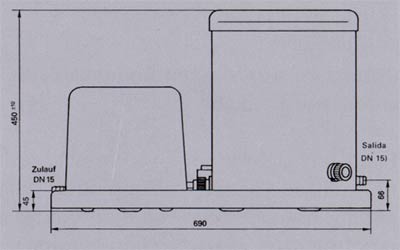
Equipo de neutralización para le caldera de condensación a gas Vertomat, a partir de 130 kW.
No hay comentarios:
Publicar un comentario