instalaciones
sábado, 14 de abril de 2012
jueves, 12 de abril de 2012
Multiplicadores de transferencia
REGISTRATE EN FOROFRIO
Multiplicadores de transferencia
Multiplicadores de transferencia de calor para las construcciones
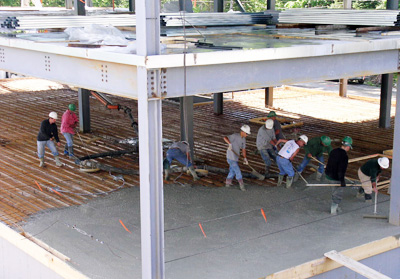
Los multiplicadores de transferencia de
calor para la mayoría de los tipos de construcción se listan en las
Tablas para calefacción y para enfriamiento que por ser tan extensa y
por falta de espacio es imposible incluirlas. Ocasionalmente se
encuentran construcciones que no están incluidas en estas descripciones
generales. Un procedimiento para determinar los multiplicadores de
transferencia de calor para las construcciones, a continuación lo
abordaremos.
CONDUCTA Y RESISTENCIA
Hay dos modos en los cuales las
características de transmisión de calor de una construcción pueden
evaluarse. La conductancia térmica es el concepto más comúnmente usado.
Expresa la cantidad de calor que fluye cada hora a través de un pie
cuadrado de una construcción por cada grado Fahrenheit de una diferencia
de temperatura.
La conductancia de una construcción
puede calcularse directamente. La aritmética involucrada en esto no es
compleja, pero puede ser confusa. La resistencia térmica es un concepto
que es más fácilmente aplicado. La conductancia y la resistencia están
directamente relacionados en que el valor U de una construcción es
igual a uno dividido por la resistencia térmica de la construcción (u=
1/R).
La resistencia térmica es la caída de
temperatura en grados Fahrenheit a través de una barrera de calor,
cuando el calor esta pasando a través de la barrera a la rata de 1,0
Btuh por pie cuadrado a la superficie por hora. Así, la resistencia
térmica se expresa en grados por Btuh por pie cuadrado. Valores
numéricos mayores de resistencia térmica indican mejor barrera de calor.
A causa de que las unidades de resistencia térmica son poco comunes,
el término de unidades de resistencia es el más comúnmente usado. Se
abrevia ur.
COMPONENTES DE LA RESISTENCIA
El concepto de resistencia térmica es
fácil de aplicar a causa de que la resistencia térmica total de una
pared o cieloraso es igual a la suma de las resistencias térmicas de
cada componente de la construcción. Para calcular la resistencia
térmica:
A. Identifique cada componente
B. Determine la resistencia térmica de cada componente
C. Añada a estas resistencia térmica para obtener la resistencia térmica total de la construcción.
B. Determine la resistencia térmica de cada componente
C. Añada a estas resistencia térmica para obtener la resistencia térmica total de la construcción.
Los componentes que deben considerarse cuando se determina la resistencia térmica de una construcción son:
A. Superficies de aire, interior y exterior.
B. Espacios de Aire – al menor de ¾ pulg. de espesor –entre materiales de construcción.
C. Materiales de Construcción incluyendo los materiales de acabado interior y exterior y el aislamiento cuando se usa.
B. Espacios de Aire – al menor de ¾ pulg. de espesor –entre materiales de construcción.
C. Materiales de Construcción incluyendo los materiales de acabado interior y exterior y el aislamiento cuando se usa.
SUPERFICIES DE AIRE
La resistencia de la superficie de aire
depende del espesor de la película de aire depende del espesor de la
película de aire que esta adyacente a la superficie. El espesor de la
película de aire depende del movimiento de aire cerca de la superficie y
de la dirección en la cual fluye el calor. Por ejemplo, la película de
aire adyacente a una superficie exterior está siendo continuamente
barrida por el viento. Consecuencialmente, no es tan gruesa como la
película de aire adyacente a la superficie interior ya que el aire del
cuarto no0 se esta moviendo tan rápidamente y hay poca o ninguna acción
de barrido. Las corrientes de aire natural también afectan el espesor
de la película de aire y crean una película más gruesa cuando el calor
fluye hacia abajo a o desde una superficie horizontal que cuando el
calor fluye hacia arriba.
Las características térmicas de la
superficie de los materiales también afectan la resistencia del aire en
la superficie. Las superficies reflectivas o brillantes tienen
resistencias térmicas mayores que las superficies no reflectivas. El
termino no reflectivo describe madera, repello, ladrillo u otros
materiales de construcción comunes. Por ejemplo, la Tabla 1, Número 1
incluye una superficie horizontal la cual tiene una resistencia térmica
de 0,61 ur, cuando el flujo de calor es hacia arriba y la superficie
es no reflectiva. Una superficie similar tiene una resistencia térmica
de 1,32 ur, sin embargo, cuando el flujo de calor es hacia arriba y la
superficie es foil de aluminio brillante. Una superficie horizontal con
el calor fluyendo hacia arriba usualmente será una superficie tal como
un cielo raso. Una superficie de foil de aluminio que encara un
espacio con ático se considera como reflectivo. Se sugiere que esta
recomendación sea seguida cuando se usa la información en la tabla 1 de
valores de resistencia para construcción y aislamiento:
La resistencia de una superficie de aire
es 1,17 ur para una superficie expuesta a un viento de 15 millas por
hora. Este valor se aplica independientemente de la dirección del flujo
de calor, la dirección en la cual está la superficie o el tipo de
material de la superficie.
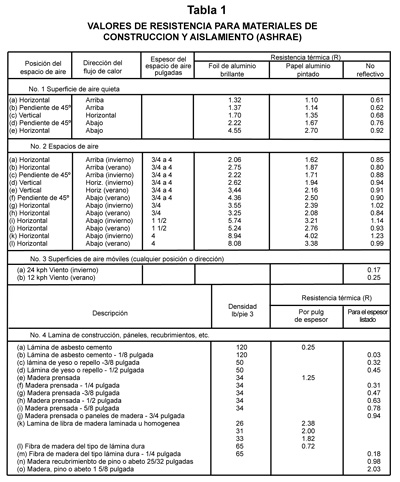
ESPACIOS DE AIRE
Un espacio de aire es aquel totalmente
encerrado de ancho y espesor limitados. Por ejemplo, un espacio formado
entres dos cuartones y las paredes interior y exterior, se considera un
espacio de aire. Un espacio de aire menor de ¾ pulg. de espesor
prácticamente no tiene valor aislante y no se considera cuando se
determina la resistencia térmica de una construcción. Así, si se instala
un aislamiento de 3 pulg. en un espacio de aire de 3 5/8 pulg. el
espacio de aire resultante sería menos de ¾ pulg. de espesor y no se
consideraría en el cálculo de resistencia térmica. La resistencia
térmica de un espacio de aire está afectada por la dirección del flujo
de calor y el tipo de material frente al espacio de aire. Por ejemplo,
la resistencia térmica de un espacio de aire vertical con flujo de calor
horizontal es 0,97 ur cuando esta frente a un material no reflectivo.
Si fuera un espacio horizontal con flujo de calor hacia arriba, la
resistencia térmica sería 0,85 ur.
Valores para espacios de aire con
diferentes tipos de superficies, se incluye en la tabla de valores
anexa. Estas superficies son foil de aluminio brillante, aluminio
pintado o papel recubierto y materiales no reflectivas. Si al menos una
superficie del espacio de aire tiene foil de aluminio brillante, el
espacio de aire se considera reflectivo se usa el valor de resistencia
mayor. Un ejemplo es un espacio de aire recubierto en un lado con lámina
de yeso que tienen su parte posterior un foil. Similarmente si un lado
del espacio de aire esta encerrado por una superficie compuesta de
papel recubierto con aluminio o pintado, se usa el valor de resistencia
para “Papel Pintado de Aluminio”. Los valores de resistencia no
reflectiva se aplican a los empaques de aire completamente encerrados
por materiales ordinarios de construcción tales como láminas de yeso,
madera, materiales de mampostería, etc.
RESISTENCIA TERMICA DE
MATERIALES DE CONSTRUCCION
MATERIALES DE CONSTRUCCION
La resistencia térmica de una pared,
cieloraso o piso es la suma de las resistencias térmicas de la
superficies de aire, los espacios de aire y los materiales de
construcción. La resistencia térmica de cada componente de construcción
depende de lo siguiente:
1. El espesor del material.
2. La habilidad del material para resistir el flujo de calor.
2. La habilidad del material para resistir el flujo de calor.
Algunos tipos de materiales de
construcción pueden usarse en muchos espesores y son uniformes a través
de este espesor tal como en el caso de un piso o pared de concreto
fundido. Así la resistencia térmica del concreto, es si resistencia por
pulgada de espesor multiplicada por el espesor de la pared en pulgadas.
Otros materiales de construcción son
comúnmente fabricados y vendidos en varios espesores estándar (tal como
madera, aislamiento fibroso, concreto y laminas aislantes). Por
ejemplo, el aislamiento fibroso a menudo es vendido en mantas o bloques
disponibles en los espesores mostrados en la tabla 2. Similarmente, la
madera usualmente se obtiene en tablas de 1,2,4 y 6 pulg. Sin embargo
las dimensiones de las tablas de madera son nominales y una tabla de 1
pulg. por ejemplo, es cerca de 25/32 pulg. de espesor. Similarmente,
una tabla de 2 pulg. tiene 1 5/8 pulg. de espesor, una tabla de 4 pulg.
tiene 3 5/8 de espesor, etc.
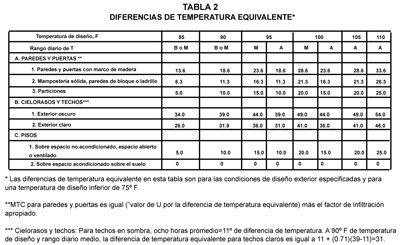
Un tercer tipo de material de
construcción se produce en tamaños estándar. Son ejemplos de este tipo
de material el ladrillo, bloque de concreto y tablón. A causa de que
estos materiales a menudo tienen agujeros incorporados en su interior,
no es posible demostrar su resistencia térmica por pulgada de espesor.
Consecuencialmente, los valores de resistencia térmica se dan para los
tamaños estándar indicados.
Las ultimas secciones de la Tabla 1
incluyen la resistencia térmica de muchos materiales de construcción.
Algunos de estos se listan para una pulgadas de espesor y otros para
espesores específicos. Por ejemplo, en el numero 4, la resistencia
térmica de la lámina de asbesto cemento aparece como 0,25 ur por
pulgadas de espesor. Sin embargo uno de los espesores más comúnmente
usados, es 1/8 pulg. y su resistencia es listada como 0,03 ur. La
resistencia térmica de materiales tales como lana mineral fibrosa se
lista sólo en la base de una pulgada de espesor. Para obtener la
resistencia térmica de este material, la resistencia por pulgada de
espesor, 3,370 ur, se multiplica por el espesor de pulgadas. El concreto
tal como el compuesto del cemento y arena y grava, el cual no ha sido
secado al horno, tiene una resistencia térmica de 0,08 ur por pulgada
de espesor. La resistencia térmica de una pared de concreto fundido de 8
pulg. es 8 x 0,64 ur.
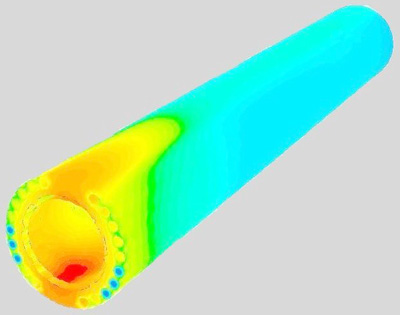
MICA DE PAREDES
Como un ejemplo del cálculo de la
resistencia térmica de una pared compuesta, considere una pared que
tiene recubrimiento exterior de madera, aislamiento de 25/32 de pulg. y
lámina de yeso de 3/8 pulg. y ½ pulg. de repello en el interior.
Para este ejemplo, el valor de U es
igual a 0,196 (1/5, 11). Cuando se redondea a dos valores decimales,
será igual a 0,20. Si se colocan dos pulgadas de aislamiento ( R-7) a
esta construcción, la resistencia térmica es 12,11 ur (5,11+7,00) y el
valor de U es 0,083 ó 0,08. Las resistencias térmica de cieloraso y
pisos se calculan en una manera similar, pero los valores de la
resistencia de los componentes varían a causa de la dirección del flujo
de calor y otros factores. Una vez que el valor de U ha sido
determinado, el multiplicador de transferencia de calor para
calentamiento se obtiene multiplicando el valor U por la diferencia de
temperatura de diseño. Para obtener el multiplicador de transferencia de
calor para enfriamiento, el valor de U se multiplica por la diferencia
de temperatura equivalente. Valores de diferencia de temperatura
equivalentes para construcciones promedio y condiciones de diseño
normales se incluyen en la Tabla 2. Los factores de infiltración que
deben considerarse cuando se calcula la ganancia de calor a través de
puertas y paredes se incluyen en la Tabla de Valores.
REGISTRATE EN FOROFRIO
¿Qué significa la clasificación “MOPD”
REGISTRATE EN FOROFRIO
¿Qué significa la clasificación “MOPD”
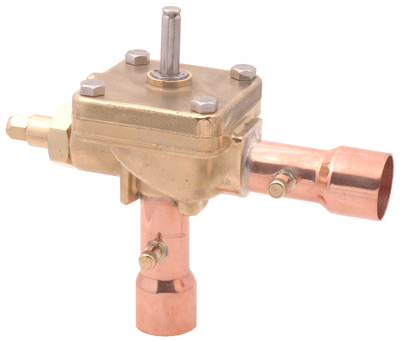
Las válvulas de solenoide están
clasificadas en términos del Máximo Diferencial de Presión de Operación
(MOPD Maximum Operating Pressure Differential por sus siglas en Inglés)
en contra del cual la válvula abrirá. Por ejemplo, con la válvula
cerrada contra una presión de entrada de 250 psi y una presión de salida
de 50 psi, el diferencial de presión a través de la válvula es de
250-50 ó 200 psi. La clasificación MOPD para la válvula es el máximo
diferencial de presión contra el cual la válvula operará confiablemente.
Si el diferencial de presión es más alto que el MOPD al que se
clasificó esa válvula, la válvula no operará.
La temperatura del devanado de la bobina y
el voltaje aplicado afectan significativamente la clasificación del
MOPD. El MOPD se reduce al aumentar la temperatura de la bobina o al
disminuir el voltaje. Por esta razón, la clasificación de MOPD se
establece operando la válvula al 85% del voltaje asignado, después de
que la bobina ha alcanzado su máxima temperatura operando a pleno
voltaje asignado.
¿Porqué algunas válvulas tienen una clasificación “Min OPD” y que significa?
Min OPD representa el Mínimo Diferencial
de Presión de Operación. Todas las válvulas operadas por piloto (como
las series 200 y 240 de Emerson) requieren una pequeña cantidad de
diferencial de presión para permitir que el pistón o el diafragma se
levanten del puerto principal. Típicamente, se requiere un diferencial
de 2 a 5 psi para lograr esto. Si el diferencial de presión es menor
que el Min OPD, entonces la válvula no operará cuando se active o
fallará en permanecer abierta. Si una válvula es considerablemente de
mayor tamaño para la aplicación, puede sufrir esta una afectación,
puesto que, la caída de presión a través de la válvula con bajos
índices de flujo puede estar por debajo del Min OPD. Los solenoides de
operación directa (como las series 50 RB Y 100 RB de Emerson) no tienen
una especificación Min OPD puesto que no dependen de las presiones del
sistema para su operación.
¿Cuáles son algunos problemas típicos que puedo esperar con una válvula solenoide y como los reconozco?
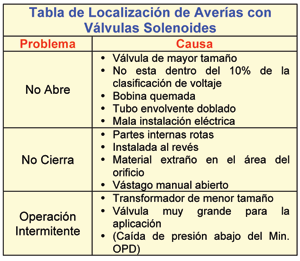
Filtrando el gasto
Filtrando el gasto

Elegir el filtro ideal que se adapte de lleno a las necesidades de su sistema de aire acondicionado puede ser complicado.
Para evitar la propagación de enfermedades en un edificio a causa de partículas aerotransportadas y mejorar la eficiencia energética se deben tener en cuenta varios factores.
La filtración del aire en sistemas HVAC es el método más usual para proteger a las personas y a los propios equipos de partículas aerotransportadas. Los filtros deben remover un rango muy amplio de tipos y tamaños de partículas, por lo que es imposible diseñar un filtro que pueda remover todos los contaminantes de manera eficaz. Incluso, dentro de una misma aplicación, muchas veces se requiere no solamente de un tipo de filtro, sino que se debe efectuar una combinación estratégica de dos o más.
En el mercado, existe una gran variedad de filtros para partículas con diferentes medidas, en espesores que pueden ir desde 1” (2.54 cm), hasta 36” (91.44 cm), y en diversas configuraciones para elegir. Cada tipo de filtro deberá satisfacer los requerimientos de calidad de aire para una aplicación específica. Así pues, la filtración de un edificio de oficinas o una tienda departamental será sumamente diferente a la de un quirófano.
Cabe señalar que los filtros de aire no representan sólo una solución al requerimiento de calidad de aire de un complejo o proceso, sino que son parte primordial para mantener la eficiencia energética nominal de los equipos HVAC. Mediante una correcta selección y un mantenimiento adecuado de filtros se evita suciedad tanto en los intercambiadores de calor (serpentines), como en el motor del ventilador, lo que evita un mayor consumo de energía en la operación. Basar la decisión de compra de filtros solamente en el precio puede resultar, a la larga, muy costoso operativamente.
Muchas de las directrices actuales recomiendan niveles de filtración basados en el estándar 52.2-2007, de ASHRAE, el cual mide la eficiencia fraccional por tamaño de partícula de un filtro HVAC. Esto indica la capacidad de un filtro para remover partículas de 0.3 hasta 10 micras de diámetro (>10 micras-visibles). La eficiencia o capacidad del filtro están determinadas por un Valor Mínimo Reportado de Eficiencia (MERV, por sus siglas en inglés), el cual se asigna a cada tipo de filtro.
Un filtro MERV 1 es el menos eficiente, mientras que un filtro MERV 16 es el más eficiente. Para protección contra partículas de 3 a 10 micras, es recomendado seleccionar filtros MERV 5-8; para protección de partículas de 1 a 3 micras, la mejor solución son los filtros MERV 9-12, y para protección de partículas contaminantes de 0.3 a 1 micra, es preciso utilizar filtros MERV 13-16. Después de considerar la eficiencia en el momento de elegir un filtro, también se deben tomar en cuenta otros parámetros que se miden en el estándar, como la caída de presión del filtro y su capacidad de retención de polvo.
Calidad del aire interior
La calidad del aire interior tiene impacto en la salud, confort y productividad de los ocupantes de un edificio. Según la Agencia para la Protección Medioambiental de Estados Unidos (EPA, por sus siglas en inglés), el aire en el interior de una edificación puede estar de 2 a 5 veces más contaminado que el del exterior.
Anualmente, se estiman pérdidas por 60 billones de dólares relacionadas con el Síndrome del Edificio Enfermo en Estados Unidos. Entre los síntomas del Síndrome, se encuentran irritación de ojos y nariz, así como dolores de cabeza asociados con el edificio propiamente y no con una enfermedad en particular. Reducir de 20 a 50% estos síntomas traería beneficios anuales de 10 a 30 billones de dólares, un incentivo muy poderoso para mejorar la calidad del aire interior.
En la Universidad de Purdue, se realizaron pruebas con el fin de cuantificar los efectos de la selección de filtros de diferentes MERV en la cantidad de polvo que traspasaría a un serpentín de enfriamiento, lo que significaría un impacto, mayor o menor, en la calidad de aire en el interior. Las mediciones se realizaron sin filtro y con filtros de cuatro diferentes MERV: 14, 8, 6 y 4, en equipos con serpentines de 3, 4 y 8 hileras (equipos de 3, 5 y 35 TR). Los resultados demostraron que los equipos con MERV altos proveen, en general, una mejor calidad de aire.
En los equipos con serpentines de 8 hileras, la cantidad de polvo que traspasó el serpentín con un filtro MERV 4 fue 30 veces mayor que el que traspasó el serpentín con un MERV 14. En la prueba sin filtro, la cantidad de polvo que traspasó el serpentín fue aproximadamente 60 veces mayor que el del filtro MERV 14. Lo anterior demuestra que la selección del MERV tendrá un impacto considerable en la cantidad de polvo que el filtro removerá o dejará pasar (ver gráfica 1).
Los edificios comerciales pueden optimizar su desempeño a través de una mejor calidad del aire si se ataca la eficiencia del filtrado. La filtración efectiva es la principal línea de defensa de los ocupantes de un edificio contra contaminantes. Una de las formas más sencillas de conseguirlo es cambiar los filtros tipo panel por filtros de superficie extendida (tipo pliegues, bolsa o minipleat). Por lo general, los filtros tipo panel (MERV 1-4) sólo remueven 20% de las partículas en el rango de 3 a 10 micras, lo que significa que están dejando pasar 80% de estas partículas relativamente grandes, además de las más finas (0.3 a 3 micras).
Algunas de las partículas en este rango de tamaño, que pueden generar reacciones alérgicas en los ocupantes de un edificio, son el polen, esporas de hongos y polvo. Las partículas que miden menos de 2.5 micras se consideran “respirables” y pueden ser inhaladas para después depositarse en los pulmones, ocasionando enfermedades y, en el peor de los casos, la muerte.
Se incluye una tabla con orientación general para la selección del nivel de filtración, publicada en La guía de calidad de aire, de la ASHRAE, un manual de mejores prácticas para el diseño, construcción y commissioning de edificios comerciales e institucionales. Las eficiencias sugeridas van desde “buenas” –parte más baja del espectro que ya representa una mejora sobre los códigos mínimos en calidad del aire interior– hasta “mejores”. Éstas últimas representan una mejoría sustancial en el beneficio sobre los niveles mínimos de los códigos (ver tabla 1).
Problema o situación
|
Recomendación/ Rango de solución
|
Resultado/Beneficio
|
Mantener las superficies de intercambio de calor y del sistema de distribución más limpias
|
Aplicar MERV 8-13
|
Reduce la excesiva suciedad del serpentín; mantiene la
eficiencia del intercambio de calor; reduce la perdida de energía;
reduce los costos de limpieza y mantenimiento; disminuye las
oportunidades para el crecimiento de moho mediante la reducción de
nutrientes y retención de humedad
|
Mantener el espacio acondicionado limpio
|
Aplicar MERV 8-13
|
Reduce las molestias ocasionadas por el polvo; reduce los costos de limpieza
|
Control de partículas viables y/o patógenas
|
Aplicar MERV 14-16
|
Reduce la exposición de los ocupantes a los patógenos
aerotransportados; disminuye efectos negativos en la salud; disminuye
al ausentismo y costos relacionados con la productividad
|
Tratar aire exterior excesivamente contaminado
|
Aplicar MERV 11-14 Aplicar fase gaseosa ME *
|
Asegura la aceptabilidad cuando el aire del exterior
es no-conforme; reduce la exposición de los ocupantes a fuentes externas
de partículas, olores e irritantes; reduce el resiego de contaminación
cruzada de los extractores del edificio; reduce los productos
indeseables de reacciones químicas entre el ozono y los químicos del
interior
|
Control específico de los contaminantes en cuestión, incluyendo los asociados con intentos criminales o accidentes
|
Aplicar MERV 13-16 Aplicar HE-HEGA *
|
Reduce el riesgo de contaminación por partículas o
gases, por derrames accidentales o incidentes criminales, que sean
perjudiciales para los procesos, productos, personas o sus actividades
relacionadas
|
Aumentar la tasa de ventilación del aire exterior
usando el procedimiento de Calidad del Aire del estándar ASHRAE 62.1
(ASHRAE 2007b)
|
Aplicar MERV 11-13 Aplicar ME-HE *
|
Puede reducir el exceso de carga latente de aire
exterior en ciertas regiones; reduce la carga de contaminantes del aire
exterior contaminado; puede resultar en disminución de la capacidad
del equipo HVAC y costos de capital relacionados, consumo de energía y
costos de operación
|
Tabla 1. ©2009 Indoor Air Quality Guide-Best Practices for Design, Construction and Commissioning, ASHRAE, Atlanta, GA.2HEPA=filtros absolutos eficiencia mínima 99.97% DOP @ 0.3 micras (“High-efficiency particulate air”)
ME=filtración molecular de eficiencia media con “by-pass” parcial HE=filtración molecular de alta eficiencia “solid bed” HEGA=adsorbente de alta eficiencia “deep bed” |
![]() |
![]() ![]() ![]() |
Gráfica 2. Gastos de operación en sistemas de climatización | |
Nota. Sin embargo, vale la pena mencionar que un proyecto de investigación reciente de la ASHRAE, relacionado con las consecuencias de la filtración en el consumo de energía, concluye que los sistemas pequeños tipo residenciales o comercial ligero no se comportan como los sistemas comerciales o industriales. Mediciones en casas y comercios pequeños, en los que se estudiaron equipos con filtros de tres rangos de eficiencias: baja (MERV 2), media (MERV 6-8) y alta (MERV 11 y 12), demostraron que elegir una filtración superior, como MERV 11, para la calidad del aire no parece tener ninguna penalización en energía (menos de 1 kW/h/ton por día) en equipos pequeños.3 |
Una necesidad constante en edificios comerciales e industriales es el ahorro energético y sus costos de operación. Después de elegir el grado de eficiencia y limpieza de aire que queremos alcanzar, la siguiente decisión es seleccionar el sistema de filtración que nos cueste menos operar durante todo el ciclo de vida útil del equipo o sistema HVAC. Según Thomas Carlsson, experto en la industria de la filtración, el costo de la energía en el que incurre un sistema de filtrado constituye 81% de su costo total, mientras que el costo del filtro per se, su instalación y los gastos de desperdicio ascienden sólo a 19%. Esto significa que el costo del filtro apenas representa una quinta parte de la inversión total (ver gráfica 2).
La caída de presión de un sistema de filtración está directamente relacionada con el consumo de energía: entre más alta sea la caída de presión, más energía se requerirá para vencer la resistencia del filtro y mover el aire a través del sistema (ver nota). Tal consideración le da especial importancia al programa de mantenimiento.
El reemplazo oportuno de los filtros también impactará en el consumo energético. La decisión de cambiar o no los filtros a tiempo impactará definitivamente en el costo de operación de todo el sistema HVAC. Puede ser muy tentador retrasar el reemplazo de filtros porque es un ahorro inmediato y tangible; pero, ¿cuál es el beneficio de retrasar una compra de filtros si se compara con el costo de la energía extra requerida para operarlos? (ver tabla 2).
Costo de retrasar el reemplazo de filtros
|
|||
Mantenimiento de rutina 4 cambios vs 3 cambios
|
|||
Mantenimiento de rutina
(trimestral)
|
Mantenimiento con retraso (un mes)
|
Impacto
|
|
Costo de los filtros inversión inicial: $70.00 mx; 100 filtros
|
$28,000
|
$21,000
|
$7,000 Ahorro en filtros
|
kWh consumidos, presupone un ∆P de 0.61” W.G. (0.22” inicial, 1.00” final)
|
217,007
|
251,695
|
34,686 Incremento en kWh
|
Costo energético: $1.40 kWh (Tarifa H-M)
|
$303,810
|
$352,369
|
$48,560 Costo adicional en energía
|
Costo total
|
$331,810
|
$373,369
|
$41,560 Incremento total
|
Tabla 2. Consumo energético en kilowatts por hora= Q x
∆Px t/n/1000; Q=flujo, ∆P= promedio de caída de presión en Pa,
t=tiempo de operación del ventilador en horas, n= producto de la
eficiencia del ventilador (68%), motor (86%) y drive (99%)
|
Un serpentín sucio no sólo produce un impacto en la capacidad de enfriamiento y la energía, también en la reproducción de bioaerosoles comunes, como esporas de bacterias y hongos, que tienden a crecer en la superficie del serpentín, afectando severamente la calidad del aire. Este problema refuerza la necesidad de proteger los serpentines con el debido nivel de filtración, el adecuado mantenimiento y el reemplazo oportuno.
Un sistema HVAC usualmente representa entre 40 y 70 por ciento de los consumos operativos de un complejo; por lo que aquellos usuarios o dueños de inmuebles que exigen y buscan la mejor tecnología en sus equipos de HVAC para asegurar el menor costo operativo deberán dedicar la misma atención a la selección adecuada de los filtros de aire, pues así protegerán el tiempo dedicado y la inversión hecha en tecnologías más costosas, pero garantizarán la salud y el confort de sus ocupantes. Al final, estarán construyendo un edificio más seguro, cómodo y sustentable.
REGISTRATE EN FOROFRIO
PROTOCOLO DE PUESTA EN MARCHA.
REGISTRATE EN FOROFRIO
PROTOCOLO DE PUESTA EN MARCHA.
Este documento pretende ser una guía de los principales pasos a seguir para la puesta en marcha de una instalación frigorífica. Desde el staff de www.forofrio.com esperamos les sea de ayuda en sus trabajos.
Es un documento general, que no puede recoger las particularidades de todas las instalaciones frigoríficas posibles. Por lo que recomendamos desde www.forofrio.com que se complemente con las instrucciones de los fabricantes y suministradores de los materiales de la instalación concreta.
ACCIONES PREVIAS AL ARRANQUE:
º Revisión de las tuberías, valvulerías y demás elementos de la instalación para comprobar que se ajusta al esquema/diseño frigorífico y reglas del arte de la refrigeración.
º Comprobación de los desagües: pendientes, sifones y resistencias de desagües en caso de que la cámara sea de temperatura bajo cero.
º Comprobación de la colocación y buen funcionamiento de las válvulas equilibradoras de presión y de las alarmas de hombre encerrado en las cámaras de temperaturas negativas.
º Comprobar que todas las válvulas de paso de la instalación estén abiertas!!!!
º Comprobación de la alimentación / acometida eléctrica al cuadro de control de la instalación:
º Tensión entre fases
º Tensión entre fase y neutro
º Ausencia de fallo de fase
º Desequilibrio de fase: máximo 2%
º Orden de las fases para el sentido de giro de los ventiladores y si el sentido de giro del compresor es único (compresores de tornillo, scroll o rotativo)
º Carga de la instalación con nitrógeno seco para:
º Realización de la prueba de estanqueidad de la instalación según lo marcado en la ITC (Institución Técnica Complementaria) correspondiente del reglamento de seguridad de plantas e instalaciones frigoríficas.
º Comprobación de fugas en la instalación: de dejara la instalación con nitrógeno el mayor tiempo posible, 24 horas como mínimo y se verificara que la presión no ha disminuido (será necesario corregir la presión si la temperatura ambiente ha cambiado). Si se detecta una bajada de la presión de nitrógeno se procederá a la búsqueda de fuga con ayuda de agua y jabón u otro elemento (véase detectores de fuga; electronicos, de llamas, o por ultrasonidos).
º Una vez solucionadas las fugas se realizara el vació de la instalación (ver documento VACIÓ EN EL SISTEMA DE REFRIGERACIÓN en este mismo foro) para eliminar los gases incondesables y la humedad presente en el circuito. Si se detecta que existe fugas porque el vació no se mantiene se debe proceder nuevamente a buscar las fugas con presión de nitrógeno.
!!!nota muy importante!!!!
No arrancar nunca un compresor con el vació con el compartimiento motor, posible daño eléctrico al bobinado:
º Realizar una primera carga incompleta de refrigerante
º Conexiones de la resistencia del carter previa la puesta en marcha para asegurar que el aceite contenga la mínima cantidad posible de refrigerante disuelto. Recomendable 14 horas antes. En todo caso, debe augurarse que la temperatura del aceite esta 15 o 20 ºC por encima de la temperatura ambiente que rodea la instalación (se puede comprobar aplicando un termómetro de contacto al carter de aceite del compresor).
º Regulación de presostatos: con una botella de nitrógeno seco y un manoreductor se procederá a la regulación de todos los presostatos de la instalación. Recordamos que las escalas de los presostatos son indicativas y no tomarse como exactas.
º Parametrización de los termostatos electrónicos y, si existen microprocesadores de control de compresores.
ºRegulación de los elementos de seguridad eléctricos (disyuntores, térmicos….) a los niveles de consumos máximos permitidos por el compresor, ventiladores etc…
º Regulación de los temporizadores de arranque de los compresores ( en caso de arranque Part-Winding o estrella-triangulo) según indicaciones del fabricante de los compresores. Regulación del resto de temporizadores del la instalación: anti corto, ciclo de compresores, temporizadores de desescarche.etc….
º Comprobación de la cadena de seguridad del compresor en el esquema eléctrico del cuadro de control de la instalación.
º Test. de funcionamiento de los volúmenes de el/los compresor/es .con la potencia quitada , comprobar que llega tensión a las Bornes de alimentación del compresor con la maniobra activada (selector de maniobra del compresor en posición marcha). En el caso de que la protección de los compresores se realice por disyuntores, será necesario puentear los contactos de maniobra del disyuntor para poder realizar este test.
º Test de funcionamiento de el/los ventiladores de la instalación. En caso de ventiladores de varias velocidades ,comprobar que la velocidad conectada es la correcta. Verificar que el sentido de giro de los ventiladores es el correcto.
º Ajuste de las bornes de potencia de compresor y ventiladores.
º Comprobar que los niveles de aceite son los correctos (si es posible) :cárter del compresor (entre/y fl del nivel del visor del càrter, deposito nodriza, de aceite(llenar al menos la mitad del volumen del deposito nodriza, ya que algo de aceite saldrá hacia la instalación para llenar los sifones y separadores de aceite).
º Colocación de los cartuchos de filtraje en líquido y aspiración si no están instalados.
º Si existen sondas de presión, comprobar que marcan lo mismo que los manómetros fijos/puente de manómetro conectado a la instalación. En caso contrario, comprobar la conexión eléctrica de la sondas.
ARRANQUE DE LA INSTALACIÓN,
º Poner el selector de maniobra del servicio frigorífico (ovarios en caso de centrales frigoríficas) en posición de marcha. Se observara que la presión de baja empieza a subir por efecto del refrigerante inyectado por la/a válvula/s de expansión. Esperar a que la presión de baja suba al menos 1 bar. por encima del tarado del presostato de baja, pero nunca por encima de la presión de evaporación máxima permitida por el campo de trabajo del compresor.
º Seguidamente, poner el selector de maniobra de 1 compresor en posición marcha. Si los pasos anteriores se han realizado, el compresor debe ponerse en marcha sin problemas.
º La presión de alta del sistema inicialmente empezara a subir y la presión de baja, bajara. Posiblemente, el sistema necesitará que se complete la carga en refrigerante con lo que es posible que el compresor pare por presostato de baja (en este caso pudiera observarse que bajn las presiones de alta y baja simultáneamente).
º Completar la carga se la instalación.
º Ir arrancando de uno en uno los compresores (si hay mas de 1, en este caso será necesario poner en marcha también mas servicios previamente).
º Comprobar que la/s cámaras y/o muebles frigoríficos descienden la temperatura. La consecución de la temperatura deseada puede llevar algún tiempo, no olvidemos que se debe enfriar los paneles, suelos, etc... En el caso de grandes cámaras de congelados, cuando se alcanza 0ºC es conveniente reducir la temperatura progresivamente de 1 a 2 ºC hasta alcanzar los -20ºC deseados.
º Comprobar el recalentamiento de cada una de las válvulas de expansión de la instalación. Regular si fuese necesario (la mayoría de las veces, si la válvula seleccionada es la correcta, el reglaje de fábrica se ajusta perfectamente).
Una vez estabilizado el funcionamiento, comprobar los siguientes datos:
º Presión de alta: debe ser coherente con la temperatura ambiente exterior (entrada de aire al condensador) el delta T de selección del condensador y el número de compresores en marcha.
º Presión de baja: debe ser coherente con el diseño de la instalación y la regulación de los compresores (si hay más de 1 o el compresor único lleva algún tipo de regulación de capacidad).
º Subenfriamiento de líquido:
º Recalentamiento de aspiración: no debe ser inferior a 5K, y no superior a 20K.
º Temperatura de descarga: mínimo 20K por encima de la temperatura saturada correspondiente a la presión de alta.
º Temperatura del aceite:
º Consumo (amperaje) de los compresores: inferior al consumo nominal de placa de características. Es recomendable comprobar que corresponde con el valor de consumo que da el fabricante en el sofware en las condiciones reales de la instalación.
º Consumo de los ventiladores: inferior o iguales a las características de la placa del ventilador.
º Voltaje
º Comprobar que el número de arranque del compresor por hora no excede el máximo permitido por el fabricante del compresor.
º Comprobar que la posición de las sondas de desescarche de los evaporadores (si existen) están colocadas en el lugar del evaporador más desfavorable a efectos de desescarche, esto es, el último sitio donde se funde el hielo. Este varía en función de diversos factores, por lo que hay que probarlo posteriormente cuando ya se ha formado hielo en el evaporador y observamos un descarche del mismo.
REGISTRATE EN FOROFRIO
VACIÓ EN EL SISTEMA DE REFRIGERACIÓN
VACIÓ EN EL SISTEMA DE REFRIGERACIÓN
¿Por qué eliminar la humedad?
º El tubo capilar o válvula de expansión quedarían obstruido por un tapón de hielo.
º La posibilidad de oxidación, corrosión y el deterioro del líquido refrigerante seria mucho mayor, el aceite envejecería mas deprisa y el aislamiento se descompondría prematuramente.
¿Por qué eliminar los incondesables?
º Aumento de la presión de condensación
º La oxidación de los materiales, aumentaría la viscosidad del aceite y por lo tanto se quemarían las válvulas.
Al hacer un buen vació del sistema, se elimina aire (y con el N2 y O2 ), así como la humedad. La relación entre el agua y el vació es muy simple, así como la relación entre la humedad y el vació: cuanto mas baja sea la presión obtenida menor humedad de agua y cantidad de aire en el sistema. Es mas difícil eliminar agua en forma liquida de un sistema que en forma gaseosa.
Para mantener la evaporación tenemos que obtener una presión mas baja que la presión del vapor del agua a la temperatura de trabajo.
TIEMPO DE VACIÓ
El tiempo de vació dependerá de:
º Volumen en m3/h de la bomba de vació
º Volumen total de los tubos.
º Volumen del sistema y tipo del mismo.
º Contenido de agua en el sistema.
º Si el vació se hace por un solo lado del sistemas o por los dos.
Se tardaría 16 veces mas lograr el vació en un nivel fijado si se usa un tubo de ¼ en lugar de uno de ½ así como el doble de tiempo si el tubo mide 2 metros en lugar de 1 metro. A menudo ,el medidor esta instalado muy cerca de la bomba de vació, donde evidentemente se mide presiones mas bajas.
El contenido de humedad es el parámetro mas variable , y al mismo tiempo es el que mas influye en el tiempo de vació. El tiempo para lograr el vació depende pues del sistema y del contenido de agua del mismo.
NIVELES DIFERENTES DE VACIÓ
Su elección dependerá de:
º Tipo y construcción del sistema
º Grados de impureza
º Tiempo necesario para conseguir el vació
SE PUEDE OBTENER DOS TIPOS DIFERENTES DE VACÍO
º A.0,05-0,1 mbar vació muy alto (desde 5.-10-2 hasta 10-1 mbar)
º B. 0,5. – 2 mbar (desde 5.-10-1 hasta 2 mbar)
Para lograr el vació entre 5.10-2 hasta 10-1 tardaremos mucho tiempo, y por lo tanto no es muy frecuente, a pesar de que ofrece la mayor seguridad. El grado mas frecuente de vació esta entre 5.10-1 y 2 mbar.
SELECCIÓN DE LAS BOMBAS
Una bomba de vació ha de ser de un tamaño que pueda hacer un nivel de vació en el sistema en un cierto tiempo. Su tamaño ha de ser adecuado para el circuito, una bomba demasiado grande puede hacer un vació en poco tiempo, pero produce formación de hielo. Al evaporar el hielo muy lentamente, tenemos la impresión de haber conseguido el vació deseado. Después de un cierto tiempo, el hielo comenzara a deshelar y evaporara, lo que aumentara la presión y, en consecuencia, encontraríamos otra vez humedad en el circuito. Por el contrario, con una bomba demasiado pequeña tendríamos un tiempo de evacuación demasiado largo.
TAMAÑO DE UNA BOMBA DE VACIÓ PARA TRABAJAR EN PLANTA
No hay ninguna ventaja en utilizar una bomba de gran tamaño en el trabajo de planta , para hacer el servicio requerido una bomba de 5 a 19 m3/h es suficiente. Para unidades mas grandes una bomba de 15 m3/h hará el mismo servicio y tan rápido como una de 85 m3/h
VALOR DEL VACIÓ
El mal funcionamiento de un grupo de refrigeración es debido a la presencia excesiva de humedad e incondesables. La presión residual ha de ser a 0,5 mbar , a la cual corresponde generalmente una cantidad aceptable de humedad. Se puede obtener una presión residual equilibrada tan solo con un sistema de vació capaz de llegar a valores tales como 10-1 hasta 3x10-1, medidos en la boca de aspiración de la bomba.
A pesar de esto , y tal y como demuestra algunas experiencias , las bombas de vació con caudales entre 3 y 15 m3/h que se has usado, hace que el tiempo de vació tenga que ser de 10 a 20 minutos , mas largo incluso para obtener el secado total del circuito.
TES DE CAÍDA DE VACIÓ:
Confirmación de que el secado se ha realizado:
Se necesita un vacuometro , cuando se ha alcanzado la presión de 0,1 mbar hasta 3,0 mbar se ha de continuar durante 10 o 20 minutos el proceso. Cerramos la válvula cerca de la bomba y se observa el vacuometro, si el sistema continua húmedo o existe una pequeña fuga , el indicador en el medidor se moverá y de este modo indicara una subida de presión en el sistema. Este tipo de tes se llama en general tes de caída de vació.
CONCLUSIONES
º La última presión óptima a la entrada de la bomba ha de ser de 0,1 hasta 0,3 mbar.
º La presión final equilibrada y estable en el circuito entero ha de ser de 2 o 3 mbar como máximo.
º El tiempo necesario de vació, una vez obtenido el vació previamente indicado, puede ser de 10 a 20 minutos.
RECONOCER LA DIFERENCIA ENTRE FUGA Y EVAPORACIÓN
LEYENDO EL VACUOMETRO
Es aconsejable controlar las condiciones del aceite de la bomba de vació después de haber realizado el segundo tes. Si el aceite se ha vuelto de color lechoso quiere decir que existe demasiada agua. Deberemos limpiar la bomba de este aceite húmedo y cambiarlo por aceite seco.
Gas Ballast es el nombre técnico de un dispositivo que se usa en las bombas rotativas de vació. Su propósito es impedir que los vapores condensen dentro de la bomba durante la acción de descarga. El dispositivo de Gas Ballast impide la condensación de vapores en la cámara de compresión de la bomba. Los vapores bombeados solo pueden ser comprimidos hasta su presión de vapor de saturación a la temperatura de la bomba. Si por ejemplo, solamente se bombea vapor de agua a la temperatura de 70ºC únicamente puede ser comprimido hasta 312 mbar. Si se sigue comprimiendo el vapor de agua se condensa sin que la presión aumente. No existe ninguna sobrepresion en la bomba, de manera que no se abre la válvula de descarga, y el agua se queda como agua de la bomba y emulsiona con el aceite de la bomba. Como consecuencia, las características lubrificantes del aceite de la bomba se deterioran muy rápidamente y la bomba puede llegar a agarrotarse si contiene demasiada agua.
El dispositivo de Gas Ballest, que fue desarrollado en 1935 por GAEDE, impide la posible condensación de vapor de agua en la bomba si se actúa de la siguiente forma.
Antes de que se empiece con la compresión, se deja entra en la cámara de compresión el lastre de aire, que es una cantidad de aire exactamente regulada, justo la cantidad que la compresión directa en la bomba haya disminuido a un máximo de 0,1 mbar. Ahora los vapores bombeados pueden ser comprimidos con Gas Ballast antes de que obtengan el punto de condensación. La presión parcial de los vapores de la bomba, de cualquier modo, no tendrían que sobrepasar ciertos valores; ha de ser tan baja que con una compresión con el factor 10, los vapores no puedan condesar a la temperatura de trabajo de la bomba. En el caso que se bombee solamente vapor de agua, este valor critico se llama tolerancia del vapor de agua.
REGISTRATE EN FOROFRIO
ELEMENTO DE EXPANSIÓN
REGISTRATE EN FOROFRIO
ELEMENTO DE EXPANSIÓN
La misión de los elementos de expansión es la de controlar el paso de refrigerante y crear burbujas de liquido para que puedan se rposteriormente evaporadas, esta es la parte que separa la zona de presión de alta con la de baja.
Tubos capilares
Los tubos capilares se utilizan habitualmente como elementos de expansión en pequeñas instalaciones normalmente comerciales, por la facilidad de instalación, el bajo coste y su fiabilidad.
Permiten la utilización de compresores de bajo par de arranque por el buen equilibrio de presiones.
Cuando el refrigerante líquido entra dentro del tubo capilar se produce una estrangulación, (aumenta la velocidad y disminuye la presión) debido a esto parte del líquido se evapora al cambiar de presión, aproximadamente un 30%.
Cuando ponemos en marcha el compresor empezamos a regar el evaporador, se evapora y va avanzando hacia el compresor, se suele colocar un termostato en la línea de aspiración antes del compresor para pararlo cuando llegue el refrigerante en estado líquido.
Al parar el compresor todo el refrigerante pasa al evaporador al no haber nada que lo impida y gracias a la diferencia de presiones.
Por esta razón no se puede utilizar recipiente en instalaciones con tubo capilar y hay que tener cuidado al dimensionar el filtro ya que este podría hacer de recipiente.
Al estar las presiones igualadas el motor arranca sin muchos esfuerzos.
Los equipos congeladores suelen llevar un separador de partículas para evitar los golpes de líquido.
El tubo está calibrado, la potencia frigorífica está en función con el diámetro y la longitud del tubo.
Ajustamos las condiciones de trabajo de los equipos con tubo capilar con la carga de refrigerante. El exceso o la ausencia de la carga de refrigerante puede ser determinante para el rendimiento del evaporador ya que la poca carga de refrigerante haría que la temperatura de evaporación sea demasiada baja y eso comporta un aprovechamiento parcial del evaporador. En cambio un exceso de carga es causa de una presión demasiado elevada y conduce a la sobrecarga del compresor pudiéndole llegar golpes de líquido.

Capilar montado junto a un evaporador
Válvulas de expansión a presión constante
La válvula de expansión a presión constante, como su nombre lo indica, mantiene una presión constante a la salida de la misma. Esta válvula sondea la presión del evaporador y cuando la misma cae por debajo del punto de control, la válvula tiende a abrir. Por el contrario cuando la presión sube por encima de este punto, la válvula cierra parcialmente.
El funcionamiento de una válvula de expansión a presión constante para una misma presión de condensación el punto de equilibrio donde la válvula de expansión alimenta tanto refrigerante al evaporador como el compresor puede bombear del mismo. Si la carga de refrigeración disminuye, también disminuye la presión de evaporación pero la válvula se resiste a esta caída abriendo. Bajo esta nueva condición el compresor se mantiene en su posición inicial y la válvula también. El evaporador se sobrealimentará en esta condición de desequilibrio.
Por el contrario si la carga de refrigeración aumenta, la presión de evaporación también aumenta y la válvula reacciona cerrándose, en este punto el evaporador se subalimentada. El uso de estas válvulas está limitado a pequeños equipos que tengan cargas relativamente constantes.
Una desventaja muy grande es que no pueden ser usadas junto con un control (presóstato de baja), ya que la condición adecuada de éste último depende en sustancia del cambio de presión en el evaporador durante el ciclo; condición que no puede esperarse de las válvulas de expansión a presión constante.
Válvulas de expansión termostáticas
El dispositivo de expansión más ampliamente usado en los sistemas de refrigeración comerciales es la válvula de expansión termostática, la cual envía el flujo refrigerante al evaporador en respuesta al grado de sobrecalentamiento del vapor refrigerante que sale del mismo.
La válvula de expansión regula el caudal de líquido refrigerante a alta presión que viene del condensador y se dirige al evaporador dejando pasar más o menos refrigerante en función del recalentamiento obtenido del bulbo sea mayor o menor.
En términos generales, la válvula de expansión es un dispositivo que se usa para regular la entrada en el evaporador del agente refrigerante en su fase líquida, procedente del condensador a través de la correspondiente tubería de líquido.
El refrigerante líquido a alta presión, que procede del condensador pasa por la válvula de expansión para convertirse en líquido a baja presión. Dicha válvula es la divisoria entre las partes de alta y baja presión del sistema.
Así, tiene dos funciones distintas: Regular la velocidad de admisión de líquido en el evaporador y por otro lado controlar la proporción de área superficial interior que se encuentra en contacto con el refrigerante líquido.
La válvula termostática, posee un elemento térmico (bulbo) conectado por medio de un pequeño tubo capilar sellado.
El principio de funcionamiento de la válvula de expansión termostática radica en mantener un recalentamiento constante en el evaporador. El bulbo está lleno parcialmente con refrigerante (será el mismo que utilice el sistema) líquido y mantiene algo de líquido en todas las condiciones de temperatura y carga, además está adaptado a la línea de succión de modo que cualquier cambio de temperatura en esta línea origine el cambio correspondiente en el bulbo térmico. Bajo un aumento de carga térmica, el refrigerante hierve con mayor rapidez en el evaporador, esto ocasiona el aumento de la temperatura en el bulbo térmico debido al recalentamiento. La mayor temperatura produce una presión superior dentro del bulbo y el tubo capilar, lo que a su vez, origina la expansión del fuelle metálico y una mayor abertura de la válvula. Como resultado se admite mayor refrigerante líquido al evaporador para compensar el aumento de carga.
El recalentamiento es un fenómeno físico y juega un papel preponderante en el tema que nos ocupa. Por un lado determina la utilización de la superficie de intercambio de calor en el evaporador y por otro provee la señal para la operación de las válvulas de expansión termostáticas.
El término "termostática" induce a pensar que la válvula mantiene una temperatura constante en el evaporador, pero en realidad ocurre todo lo contrario, al variar la capacidad del sistema con un compresor de desplazamiento constante la presión del evaporador varía a la capacidad máxima, la válvula se abre completamente y la presión toma un cierto valor. Al decrecer la capacidad, la válvula se cierra y la presión decrece hasta que se establece un valor correspondiente a la combinación del compresor y la válvula.

aspecto de dos válvulas de expansión termostáticas



Válvulas de expansión de diferentes potencias

Orificio de válvula de expansión de gran potencia
Las válvulas de expansión termostática incorporan, como ya hemos citado, un elemento termostático que consta de un diafragma, capilar y el bulbo que para su colocación, hay unas normas importantes a seguir, ya que de no ser así puede ocasionarnos fallos en su funcionamiento.
El bulbo debe estar bien en contacto con la tubería de aspiración, no debe ir con cinta aislante o tiras de plástico, se debe colocar con la presilla metálica que suele acompañar el fabricante cuando la suministra.
Colocarlo en una superficie limpia y lisa, no se debe colocar sobre un codo, curva o soldadura para asegurar una buena conducción calorífica.
El bulbo tiene una hendidura que es la que se aloja sobre el tubo.
La colocación del tubo será siempre a contracorriente de la dirección del refrigerante . No colocar el bulbo en la parte baja del tubo ya que por esa parte es por donde circula el aceite que hace de capa aislante. Se debe colocar entre las 2 y las 4.

Puntos de colocación correcta del bulbo con respecto al tubo de aspiración
El tubo de compensación exterior si existe debe estar entre 10 o 15 cm después del bulbo.
Válvula de expansión termostática con compensador o igualador de presión
Esta válvula posee un igualador de presión, cuya existencia se justifica al considerar que en ciertos evaporadores, particularmente en aquellos de gran capacidad, existen pérdidas de presión. En general, este igualador de presión puede ser interior (en el mismo cuerpo de la válvula) o exterior (con conexiones fuera de la misma). En el primer caso, dicho igualador consiste en un paso en el interior de la válvula que comunica la presión de aspiración al fuelle por debajo, balanceando así la presión de trabajo de la válvula y evitando que las altas presiones que se originan en la aspiración por inundación del evaporador a la puesta en marcha, afecten la regulación de la válvula de expansión. En las válvulas con igualadores de presión exterior, esta comunicación se consigue por medio de un tubo conectado desde la cámara debajo del fuelle hasta la línea de aspiración después del punto donde hace contacto el bulbo de la válvula.
La conclusión es que se utilizara el compensador de presión con evaporadores que presenten una importante perdida de carga.
Válvula de expansión con distribuidores
Este elemento asegura una distribución del refrigerante dividido por el evaporador en varias secciones donde conseguimos un mayor rendimiento ya que reducimos las pérdidas de carga y se mantiene una temperatura de salida del evaporador más uniforme.
Para la utilización de un distribuidor con un buena alimentación de las distintas secciones del evaporador se deben seguir ciertas normas:
Utilizar válvula de expansión con igualación de presión externa.
Todas las secciones del evaporador deben tener la misma perdida de carga.
Que la carga calorífica de cada sección sea idéntica para obtener una evaporación uniforme en cada sección.
Válvulas de expansión con carga MOP
Una desventaja de las válvulas de expansión termostáticas convencionales es la de abrirse por completo y sobrealimentar al evaporador durante el arranque de los ciclos del compresor.
Esto es motivado porque la presión en el evaporador cae rápidamente cuando arranca el compresor y la presión en el bulbo permanece alta, hasta que desciende y alcanza la temperatura de operación normal.
La potencia del compresor aumenta con la temperatura del evaporador ó presión del evaporador. En los momentos de arranque después de una larga parada ó después del desescarche y especialmente cuando se trabaja con bajas temperaturas se hace necesario limitar la presión de aspiración ó en su defecto sobredimensionar el compresor para estos períodos "si bien cortos" de arranque.
Una de las formas de limitar la presión de aspiración para evitar colocar un compresor de mayor potencia es colocar una válvula de expansión termostática con carga MOP (Máxima Operación de Presión).
La válvula de expansión con carga MOP es idéntica a la de expansión termostática común e incluso tiene el bulbo cargado con el mismo tipo de fluido, lo único que varía es la cantidad de éste. La cantidad de líquido es tal que a una predeterminada temperatura este líquido se ha vaporizado y por encima de este punto el incremento de temperatura tiene muy poca influencia sobre el elemento termostático.
Válvula de expansión electrónica
Las válvulas de expansión electrónicas, éstas se pueden clasificar en varios tipos de acuerdo al tipo de construcción y funcionamiento.
Uno de estos tipos es la válvula de expansión electrónica que modula en base a pulsos de ancho variable que se consiguen mediante el control electrónico. Esta válvula es del tipo solenoide, es decir ON-OFF. Si bien ella está totalmente abierta ó totalmente cerrada, actúa como un dispositivo de regulación modulante variando el tiempo que permanece abierta ó cerrada. Por ejemplo, si la válvula cicla cada 10 segundos y es necesario un 40% del fluido la válvula estará abierta 4 segundos y cerrada 6 segundos. Si el fluido necesario fuera del 50% la válvula estará abierta 5 segundos y cerrada otros 5 segundos.
Otro tipo de válvula de expansión electrónica es la que se conoce como "HEATMOTOR VALVE"ó "THERMAL MOTOR VALVE". La operación de esta válvula es controlada por un controlador electrónico el cual en respuesta a las señales de 2 sensores S1 y S2 controla la cantidad de energía suministrada al elemento de calefacción en el actuador de la válvula. El valor requerido de recalentamiento se puede variar fácilmente por medio de una perilla en un rango que por ejemplo puede ir desde 2º C hasta 18º C. Si el grado de recalentamiento actual no es igual al requerido por la válvula, el controlador envía una señal en forma de pulsos eléctricos al elemento calefactor el cual causará la apertura ó cierre de la válvula.

Válvulas de expansión electrónicas
REGISTRATE EN FOROFRIO
COMPRESORES
REGISTRATE EN FOROFRIO
COMPRESORES
Máquina que eleva la presión de un gas, un vapor o una
mezcla de gases y vapores. La presión del fluido se eleva reduciendo el
volumen específico del mismo durante su paso a través del compresor.
Comparados con turbo soplantes y ventiladores centrífugos o de
circulación axial, en cuanto a la presión de salida, los compresores se
clasifican generalmente como maquinas de alta presión.
Los compresores se emplean para aumentar la presión de una gran variedad de gases y vapores para un gran número de aplicaciones. La utilidad que estamos estudiando es la del compresor de refrigeración, empleado para comprimir el gas del vaporizador. Otras aplicaciones abarcan procesos químicos, conducción de gases, turbinas de gas y construcción.
Tipos de compresores: Alternativo, rotativo, tornillo, centrífugos y scroll.
Estos se pueden clasificar en:
Compresor hermético
Este fue desarrollado en un esfuerzo para lograr una disminución de tamaño y costo y es ampliamente utilizado en equipo unitario de escasa potencia. Como en el caso del moto-compresor semihermético, el motor eléctrico se encuentra montado directamente en el cigüeñal del compresor, pero el cuerpo es una carcasa metálica sellada con soldadura.
Estos compresores en caso de avería, son reemplazados debido a la inaccesibilidad por el tipo de fabricación.
La aplicación de estos compresores va desde pequeñas potencias como neveras, equipo comerciales, pasando por aires acondicionados domésticos de distintas potencias hasta pequeñas plantas enfriadoras de potencias considerables.
Los compresores se emplean para aumentar la presión de una gran variedad de gases y vapores para un gran número de aplicaciones. La utilidad que estamos estudiando es la del compresor de refrigeración, empleado para comprimir el gas del vaporizador. Otras aplicaciones abarcan procesos químicos, conducción de gases, turbinas de gas y construcción.
Tipos de compresores: Alternativo, rotativo, tornillo, centrífugos y scroll.
Estos se pueden clasificar en:
Compresor hermético
Este fue desarrollado en un esfuerzo para lograr una disminución de tamaño y costo y es ampliamente utilizado en equipo unitario de escasa potencia. Como en el caso del moto-compresor semihermético, el motor eléctrico se encuentra montado directamente en el cigüeñal del compresor, pero el cuerpo es una carcasa metálica sellada con soldadura.
Estos compresores en caso de avería, son reemplazados debido a la inaccesibilidad por el tipo de fabricación.
La aplicación de estos compresores va desde pequeñas potencias como neveras, equipo comerciales, pasando por aires acondicionados domésticos de distintas potencias hasta pequeñas plantas enfriadoras de potencias considerables.



Compresores hermético

Compresor hermético imagen interior
Compresor semihermético
Este tipo de compresores fue iniciado por Copeland y es utilizado ampliamente en los populares modelos Copelametic. El compresor es accionado por un motor eléctrico montado directamente en el cigüeñal del compresor, con todas sus partes, tanto del motor como del compresor, herméticamente selladas en el interior de una cubierta común.
Se eliminan los trastornos del sello, los motores pueden calcularse específicamente para la carga que han de accionar, y el diseño resultante es compacto, económico, eficiente y básicamente no requiere mantenimiento. Las cabezas cubiertas del estator, placas del fondo y cubiertas de cárter son desmontables permitiendo el acceso para sencillas reparaciones en el caso de que se deteriore el compresor.
Este tipo de compresores fue iniciado por Copeland y es utilizado ampliamente en los populares modelos Copelametic. El compresor es accionado por un motor eléctrico montado directamente en el cigüeñal del compresor, con todas sus partes, tanto del motor como del compresor, herméticamente selladas en el interior de una cubierta común.
Se eliminan los trastornos del sello, los motores pueden calcularse específicamente para la carga que han de accionar, y el diseño resultante es compacto, económico, eficiente y básicamente no requiere mantenimiento. Las cabezas cubiertas del estator, placas del fondo y cubiertas de cárter son desmontables permitiendo el acceso para sencillas reparaciones en el caso de que se deteriore el compresor.



Compresor semihemético en tamdem Compresor semihermetico de gran caballaje

Compresor de pequeño caballaje para cámara frigorífica
Compresores abiertos
Su principal singularidad es que el motor y compresor van separados. Son estos compresores los pioneros en equipos de refrigeración Con los pistones y cilindros sellados en el interior de un cárter y un cigüeñal extendiéndose a través del cuerpo hacia afuera para ser accionado por alguna fuerza externa que normalmente esta fuerza es por transmisión a través de correas a un motor. Tiene un sello en torno del cigüeñal que evita la pérdida de refrigerante y aceite del compresor.
Como desventajas podemos citar su mayor peso, costo superior, mayor tamaño, vulnerabilidad a perdidas de los sellos, difícil alineación del cigüeñal, ruido excesivo y corta vida de ciertos elementos.
Este compresor ha sido reemplazado por el de tipo semihermético y hermético, y su uso continua disminuyendo a excepción de aplicaciones especializadas como es el acondicionamiento de aire para automóviles.
Su principal singularidad es que el motor y compresor van separados. Son estos compresores los pioneros en equipos de refrigeración Con los pistones y cilindros sellados en el interior de un cárter y un cigüeñal extendiéndose a través del cuerpo hacia afuera para ser accionado por alguna fuerza externa que normalmente esta fuerza es por transmisión a través de correas a un motor. Tiene un sello en torno del cigüeñal que evita la pérdida de refrigerante y aceite del compresor.
Como desventajas podemos citar su mayor peso, costo superior, mayor tamaño, vulnerabilidad a perdidas de los sellos, difícil alineación del cigüeñal, ruido excesivo y corta vida de ciertos elementos.
Este compresor ha sido reemplazado por el de tipo semihermético y hermético, y su uso continua disminuyendo a excepción de aplicaciones especializadas como es el acondicionamiento de aire para automóviles.

















Visión interior compresor abierto
Compresor rotativo
Este compresor sustituye el movimiento alternativo de los pistones por el movimiento circular de una excéntrica. En primer lugar hay que decir que el motor y el compresor quedan dentro de sobre el carter de plancha de acero soldado, donde en este carter existen unas aletas de enfriamiento. La parte de compresión y el rotor van fijados en columna vertical común. Así como ya hemos citado el gas que es aspirado entra el la cavidad cilíndrica empujado por una excéntrica comprimiendo y descargando por una perforación longitudinal (línea de descarga) que recorre el conjunto del compresor, por esta razón en estos compresores observaremos alta temperatura dentro del compresor.
Por su método de compresión obtiene mucho más rendimiento que el compresor de simple efecto. Siempre se montan acompañados de un pequeño depósito de aspiración o separador de partículas.
Encontraremos el compresor rotativo instalado en equipos domésticos de aire acondicionado mayoritariamente.
Como dato estos compresores recibían el nombre de compresor hermético Frigidaire.
Este compresor sustituye el movimiento alternativo de los pistones por el movimiento circular de una excéntrica. En primer lugar hay que decir que el motor y el compresor quedan dentro de sobre el carter de plancha de acero soldado, donde en este carter existen unas aletas de enfriamiento. La parte de compresión y el rotor van fijados en columna vertical común. Así como ya hemos citado el gas que es aspirado entra el la cavidad cilíndrica empujado por una excéntrica comprimiendo y descargando por una perforación longitudinal (línea de descarga) que recorre el conjunto del compresor, por esta razón en estos compresores observaremos alta temperatura dentro del compresor.
Por su método de compresión obtiene mucho más rendimiento que el compresor de simple efecto. Siempre se montan acompañados de un pequeño depósito de aspiración o separador de partículas.
Encontraremos el compresor rotativo instalado en equipos domésticos de aire acondicionado mayoritariamente.
Como dato estos compresores recibían el nombre de compresor hermético Frigidaire.

compresor rotativo

esquema partes mecánicas de compresor rotativo



Partes mecánicas aspiración compresor rotativo Parte de descarga de compresor rotativo
Compresor scroll
Su aspecto exterior es similar al compresor rotativo. La diferencia con respecto a estos difiere en el método de compresión. Este compresor comprime utilizando dos espirales como puede observarse en las fotografías, una se encuentra fija y la otra se desplaza sobre ésta, disminuyendo el volumen y realizando una compresión continua, lo cual hace que su rendimiento aumente considerablemente.
Su aspecto exterior es similar al compresor rotativo. La diferencia con respecto a estos difiere en el método de compresión. Este compresor comprime utilizando dos espirales como puede observarse en las fotografías, una se encuentra fija y la otra se desplaza sobre ésta, disminuyendo el volumen y realizando una compresión continua, lo cual hace que su rendimiento aumente considerablemente.



Por otro lado este compresor tiene pocas partes móviles
por lo que disminuye la vibración y el ruido y tiene tolerancia en la
admisión de refrigerante en forma de líquido.



Partes interiores del compresor scroll

Compresor scroll
Compresor tornillo
Se utilizan para obtener potencias frigoríficas que los compresores de pistón no son capaces de alcanzar.
Esta formados por dos husillos helicoidal donde del espacio resultante entre se produce la compresión.
Los husillos helicoidales se nombran como primario, provisto de 4 pasos de perfil semicircular y secundario provisto este de 6 pasos. En el espacio resultante es donde a medida que avanza el refrigerante es donde se produce la compresión.
Se utilizan para obtener potencias frigoríficas que los compresores de pistón no son capaces de alcanzar.
Esta formados por dos husillos helicoidal donde del espacio resultante entre se produce la compresión.
Los husillos helicoidales se nombran como primario, provisto de 4 pasos de perfil semicircular y secundario provisto este de 6 pasos. En el espacio resultante es donde a medida que avanza el refrigerante es donde se produce la compresión.

Como elemento imprescindible encontramos en todos estos compresores los separadores de aceite
Este tipo de compresor es de apertura gradual a través de la ventana de aspiración del compresor desde el 10% hasta el 100%, esta regulación se lleva a cabo con un pistón de capacidad que abre o cierra el espacio entre los dos tornillos. Son bastante ruidosos y aceptan retornos de líquido, aceptan temperaturas altas de descarga.

Sección de un compresor de tornillo

REGISTRATE EN FOROFRIO
Suscribirse a:
Entradas (Atom)